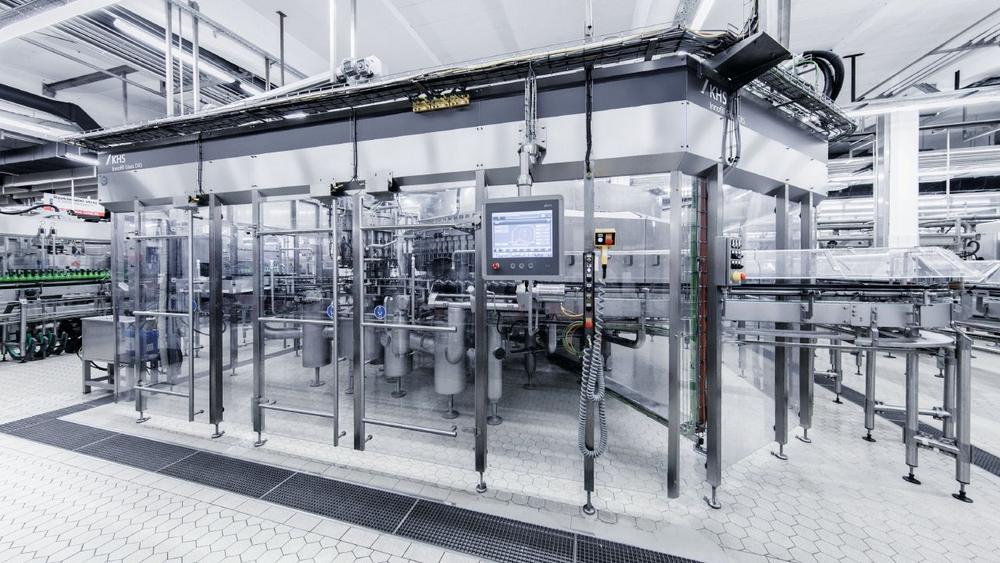
“Successful open-heart surgery”: Pyraser Landbrauerei invests in a KHS glass bottle filler
Seven days from ingress to production start was the clear instruction from Pyraser Landbrauerei – one that KHS followed to the letter. “It was successful open-heart surgery where nothing was allowed to go wrong,” smiles master brewer Helmut Sauerhammer. The brewery had gradually renewed its bottle cellar and in the process invested in a KHS Innofill Glass DRS glass bottle filler. Among other aspects, the decision-makers at the Franconian brewery were quickly convinced by the machinery’s consumption values and the low-oxygen filling process so essential when bottling beer. The patented KHS DRS-ZMS filling system uses just 210 grams of CO2 per hectoliter of beer. “We need a lot less carbon dioxide than the usual quantity common to the market to yield the same or even better residual oxygen values,” states Mike Herrmann, KHS Sales Germany and the man responsible for the project.
Another special feature at the country brewery is that Pyraser closes its beer bottles with aluminum caps. Because of this and the greater volume more oxygen would normally be pressed into the bottle compared to the amount required with classic crown corks; this would be detrimental to the beer as the product would then age more rapidly. To minimize oxygen pickup, the KHS glass filler therefore blasts the aluminum roll-on caps with CO2 in the capper. This joint development with the brewery means that the very good oxygen values in the bottle are the same as those for crown corks.
Efficiency boosted by automated CIP caps
Furthermore, the Innofill Glass DRS works with automatic CIP caps. “On the one hand, cleaning is considerably simplified as a lot less effort is needed for operation. On the other, the time saved as a result boosts efficiency in production,” Sauerhammer says. The number of manual interventions is reduced, as are toolless format changeovers thanks to hygienic QUICKLOCK fast-acting locks. The program is automatic and operated at the press of a button. Up until now employees had to place the CIP caps on the filling valves by hand. Cleaning processes can now be preset for specific times. They start automatically, with no manual intervention necessary. Any potential contamination of the filler, as could be the case where CIP caps are applied manually, is also prevented.
Water consumption significantly reduced
The new investment is also convincing with regard to sustainability. With its separate cooling circuit the ECO vacuum pump significantly reduces water consumption, meaning that Pyraser Landbrauerei uses only 80 liters an hour instead of the previous 800.
With the Innofill Glass DRS breweries profit from cutting-edge technology from the high-performance range and from a clearly structured machine design which considerably facilitates both operation and the entire production process. Pyraser Landbrauerei fills up to 26,000 bottles of beer or a maximum of 24,000 bottles of soft drinks per hour – with no hitches whatsoever since commissioning, Sauerhammer claims. “I’ve never known the first filled product to be ready for sale as quickly as here. We’re delighted!"
KHS GmbH is one of the leading manufacturers of filling and packaging systems for the beverage, food and non-food industries. The KHS Group includes the following companies: KHS GmbH, KHS Corpoplast GmbH, and numerous subsidiaries outside Germany, located in Ahmedabad (India), Sarasota and Waukesha (USA), Zinacantepec (Mexico), São Paulo (Brazil) and Suzhou (China).
KHS GmbH manufactures modern filling and packaging systems for the high-capacity range at its headquarters in Dortmund, Germany, and at its factories in Bad Kreuznach, Kleve and Worms. The group’s PET expertise is pooled at KHS Corpoplast GmbH in Hamburg, Germany, where innovative PET packaging and coating systems are developed and produced. KHS is a wholly owned subsidiary of the SDAX-listed Salzgitter AG corporation. In 2019 the KHS Group and its 5,149 employees achieved a turnover of around €1.260 billion.
KHS GmbH
Juchostr. 20
44143 Dortmund
Telefon: +49 (231) 569-0
Telefax: +49 (231) 569-1541
http://www.khs.com
Presse- und Öffentlichkeitsarbeit
Telefon: +49 (251) 625561-243
E-Mail: deppe@sputnik-agentur.de
