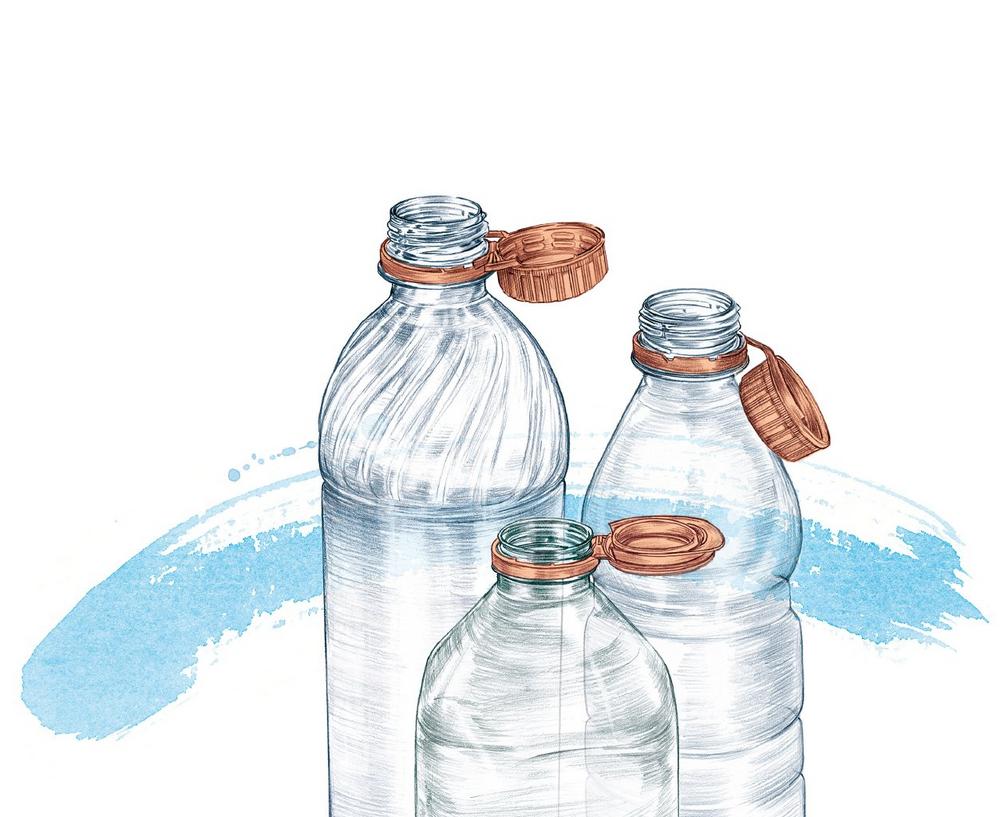
EU tethered caps directive: KHS provides holistic advice on possible measures and line adaptations
The directive is part of the EU Plastics Strategy that aims to reduce the number of single-use plastic items most frequently found in the environment. The EU counts loose caps from one-way PET beverage bottles among the aforementioned items. Article 6 of the directive specifies that tethered caps are a requirement that must be implemented by July 2024. All producers of soft drinks, still water products, aseptic beverages and beer in the EU must convert their machinery to this end by the appointed date. At the moment bottle cap standards valid throughout Europe are being prepared in order to simplify the introduction of the directive for all member states. The proposed directive is expected to pass into law in the near future. “The uncertainty in our branch of industry can be clearly felt, for implementing this accordingly at production plants also depends on the nature of fixed standards – and time is of the essence here,” says Armin Wille, head of Service Sales at KHS.
Comprehensive KHS service concept facilitates conversion
Implementing the directive simultaneously in 27 member states is a unique undertaking and huge feat for beverage, cap and preform manufacturers and all associated suppliers to master. “Our customers are concerned and have to know in good time about the possible action and investments they need to take and make with respect to the regulatory decisions,” Wille explains. The turnkey supplier has thus devised a service concept that shows in technical detail which conversions are required on PET stretch blow molder and filler/capper combinations for which capping systems. “We’re familiar with the valid legal provisions and the caps and closures these affect in combination with the respective containers. The same applies to the markets and KHS machines that are able to process all designs – except non-rotationally symmetrical closures,” Wille continues. “We offer our customers an optimum, individual technical system suitable for the relevant application that caters for all of the above.”
In order to provide comprehensive, holistic and expert advice when it comes to the bottle design, KHS Service works closely with the Bottles & Shapes™ experts at KHS. Together they analyze customer requirements and consult on the implementation of all conversion measures. This means that KHS can show bottlers all of the key parameters for the necessary technical systems, allowing the latter to make future-proof investments in the market well in advance.
Simple cap change or new bottle design?
The solutions on offer that cater for the new directive range from changing the existing cap type over to a tethered cap variant through developing a lighter cap standard to examining the PET container as a whole above and beyond the legal requirements. “We study all of the bottle parameters in great detail and advise our clients on possible further savings in weight or other adaptations with a view to producing a sustainable design,” says Wille. The main aim is to generate extra added value in the long term by saving on resources. Here, KHS also has pending EU directives firmly in its sights that will also play a role for the beverage industry in the near future. By 2025, for instance, the EU requires that PET bottles comprise 25% recyclate, with this amount rising to 30% by 2030.
Under the umbrella of its Bottles and Shapes™ PET container consultancy service, KHS helps beverage producers to implement their objectives and adjust their portfolio where necessary. “Now’s a good time for bottlers who haven’t yet redesigned their containers to invest in the future and see the obligatory provisions of the EU directive as an opportunity. By reducing the bottle weight and using less material as a result, we can save even more resources and thus money,” Wille smiles.
Cost consultancy for initial investments
To assist customers planning an initial investment, KHS clearly outlines which costs bottlers should expect, calculating their return on investment in advance. Together with its local, national and global customers, the systems provider draws up both a cost estimate and the savings expected thanks to the use of less PET. “This can turn an obligatory legal requirement into a starting point for innovative new products, at the same time saving on resources and permanently cutting CO2 emissions in production,” Wille states. “We offer decades of expertise here and have extensive experience in this field with and without recourse to EU specifications. Format conversions and container design are two of our core areas of expertise. Here, we demonstrate the kind of added value we offer our customers throughout the entire value creation process, thus strengthening their product and brand position on the market,” he concludes.
The KHS Group is one of the leading manufacturers of filling and packaging systems for the beverage and liquid food industries. The KHS Group includes the following companies: parent company KHS GmbH and numerous subsidiaries outside Germany, located in Ahmedabad (India), Waukesha (USA), Zinacantepec (Mexico), São Paulo (Brazil) and Suzhou (China). KHS manufactures modern filling and packaging systems for the high-capacity range at its headquarters in Dortmund, Germany, and at its factories in Bad Kreuznach, Kleve, Worms and Hamburg. The KHS Group is a wholly owned subsidiary of the SDAX-listed Salzgitter AG corporation. In 2019 the KHS Group and its 5,149 employees achieved a turnover of around €1.260 billion
KHS GmbH
Juchostr. 20
44143 Dortmund
Telefon: +49 (231) 569-0
Telefax: +49 (231) 569-1541
http://www.khs.com
Presse- und Öffentlichkeitsarbeit
Telefon: +49 (251) 625561-243
E-Mail: deppe@sputnik-agentur.de

