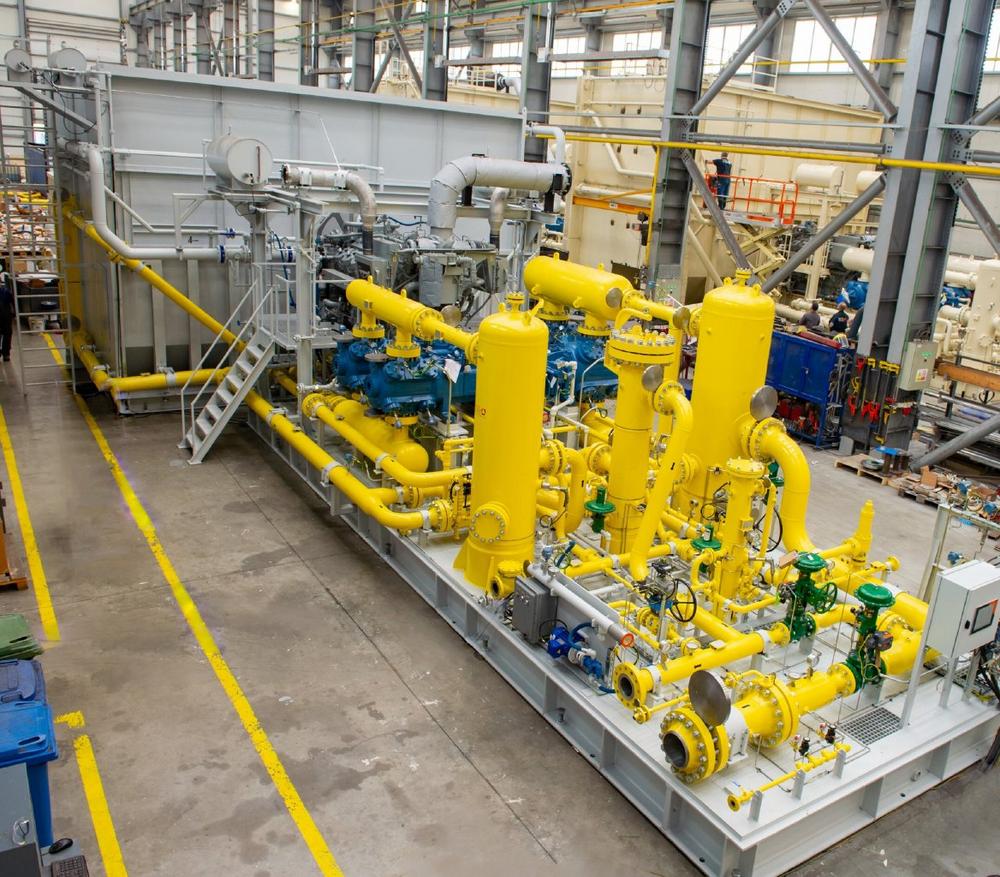
Ziel erfüllt: „Qualitativ bessere Produkte in kürzerer Zeit und zu besseren Kosten“
Im Herzen des Siebenbürgischen Beckens gelegen, liegt die rumänische Stadt Chirileu. Hier ist die Heimat von Euro Gas Systems (EGS), einem Hersteller von Gaskompressor-Paketen. EGS ist ISO 9001-zertifiziert und offizieller Distributor und Packager für Ariel Kolbenkompressoren, „Platinum Solution Provider“ für die Gasmotoren des renommierten Herstellers Waukesha sowie OEM für Caterpillar und andere namhafte Anbieter. Das Unternehmen bietet erstklassige Kompressorenlösungen für die Märkte in Europa, dem Mittleren Osten, Afrika, Asien und der GUS. Dabei kommt ein umfangreicher Maschinenpark mit CNC-Schneid-, Schweiß-, Bohr- und Walzmaschinen, einer Abkantpresse, vertikalen und horizontalen Bearbeitungszentren sowie eigenen Färbeanlagen und Sandstrahlkammern zum Einsatz.
Mit mehr als 30 Jahren Know-how betreibt das Unternehmen drei Produktionsstätten mit einer Gesamtfläche von über 9.000 qm und einer Bürofläche von 1.300 qm. Neben dem Packaging von Kolbengaskompressoren umfasst das Produktportfolio von EGS auch Gas-to-Power-Lösungen für die Öl- und Gasindustrie, luftgekühlte Wärmetauscher (ACHE) und Druckbehälter mit PED- und ASME-Zertifizierungen. Mit jahrzehntelanger Erfahrung, vielseitigen internen Ressourcen und erstklassiger Infrastruktur sind die von EGS angebotenen Produkte maßgeschneidert und bieten eine große Flexibilität bei der Integration auch kundenspezifischer Spezifikationen. Der Fokus auf den Ausbau der hauseigenen Engineering-Fähigkeiten und Dienstleistungen war auch ein treibender Faktor für EGS bei der Anschaffung neuer Maschinen.
„Eines der Ziele unseres Unternehmens ist es, die Effizienz in allen Produktionsprozessen zu steigern, damit wir qualitativ bessere Produkte in kürzerer Zeit und zu besseren Kosten herstellen können", sagt Roger Wachter, Geschäftsführer von EGS, der die Entscheidung traf, im Laufe des Jahres 2020 in eine multifunktionale CNC-Schneidmaschine zu investieren. Die Wahl fiel auf MicroStep, da der Anbieter von Schneid- und Automationslösungen eine Maschine für die Bearbeitung aller geforderten Arten von Halbfabrikaten anbieten und zudem Erfahrung mit ähnlichen multifunktionalen Schneidsystemen nachweisen konnte. „Bei dieser Investition wurden alle 3 Ziele erfüllt, so dass die Entscheidung leichtfiel; auch mit Blick auf den möglichen ROI (Return on Investment)", so Wachter.
Universalmaschine für EGS
Entsprechend den komplexen technischen Anforderungen von EGS wurde ein universelles und robustes CNC-Portalschneidzentrum auf Basis von MicroSteps DRM maßgeschneidert konfiguriert. Die Maschine besteht aus drei separaten Zonen: einer Sektion zur Bearbeitung von Blechen und Behälterböden, einer Zone für Rohre und geschlossene Profile sowie einer Sektion zur Trägerbearbeitung. Über jeder der Zonen arbeitet ein Schwerlastportal, das mit drei Werkzeugstationen ausgestattet ist: einem 3D-Plasmarotator „Pantograph“ (schwenkbar bis zu 120°), einem Autogenrotator zum Fasenschneiden bis zu 65° und einem 3D-Laserscanner. Die Maschine kombiniert 3D-Plasma- und 3D-Brennschneidtechnologie zur Schweißnahtvorbereitung mit intelligenten Scanfunktionen. „Mit dem laserbasierten Scanner passt die Maschine ihren Schneidpfad automatisch an, um produktionsbedingte etwaige Abweichungen der Geometrien aufgrund von Frästoleranzen zu berücksichtigen", erklärt Wachter. „Die endgültigen Schnitte sind bemerkenswert mit sauberen Fasen. Diese erfordern nur eine geringe Nacharbeit vor dem Einpassen und Schweißen."
Ein typisches Beispiel für die Vorteile, die eine solche Maschine für Hersteller wie EGS bringt, ist eines der gängigsten Produkte: die zweistufige Kompressoreinheit Ariel KBK4. Deren Herstellung erfordert präzises Schneiden mit Schweißnahtvorbereitungen an Blechen, Rohren, Behälterböden sowie verschiedenen Arten von offenen Profilen.
Fasenschneiden von Blechen und Behälterböden mit Plasma und Autogen
Der Blech- und Behälterbodenschneidbereich des Multifunktionscenters besteht aus einem Schneidtisch mit einer Arbeitsfläche von 6 x 2,5 m, der das Plasmaschneiden von Blechen im Dickenbereich von 2 bis 80 mm und das Autogenschneiden von 10 bis 150 mm ermöglicht. Auf der Arbeitsfläche kann auch ein Behälterboden mit einem Durchmesser bis 2.000 mm und einer Höhe von 600 mm platziert und sowohl mit Plasma als auch mit Autogen geschnitten werden. Dank des 5-achsigen Plasmarotators „Pantograph“ können mit der Hypertherm Plasmastromquelle HPR400xD (400A) Konturen in die gesamte Behälterbodenoberfläche geschnitten sowie auch Fasen für die Schweißnahtvorbereitung exakt eingebracht werden. Nach dem Schneidprozess werden die Behälterböden auf Rohre geschweißt, um Druckbehälter – zum Beispiel Kompressor- Druckausdehnungsgefäße, herzustellen.
Da reale Behälterböden in der Regel produktionsbedingte Abweichungen von der zugrundeliegenden Idealkontur ihrer 3D-Modelle aufweisen, die für die CAM-Programmierung verwendet werden, liegt der Schlüssel zur präzisen Bearbeitung darin, die reelle Oberflächengeometrie und die Abmessungen jedes Werkstücks zu identifizieren, den eine Maschine schneiden soll. Zu diesem Zweck hat MicroStep ein einzigartiges 3D-Laserscanning-Verfahren mit Punktwolkenabbildung entwickelt (MicroStep mScan Technologie), das es ermöglicht, die wahre Form eines Behälterbodens zu ermitteln und diese Messung für die anschließende Anpassung des generierten Schneidprogramms zu verwenden, um der Behälterbodenoberfläche genau zu folgen. Dazu wird der Scanner in einer schwenkbaren Drehhalterung auf einer separaten Werkzeugstation mit einem Z-Hub von bis zu 1,5 m platziert. Neben Behälterböden wird er auch zum Scannen von Rohren, Profilen und Trägern eingesetzt.
Schneiden von Rohren bis 2.000 mm Durchmesser
Der Bereich zum Schneiden von Rohren und Hohlprofilen befindet sich hinter dem Schneidtisch. Er ermöglicht das Fasenschneiden von Rohren in einer relativ großen Spanne von Durchmessern, die von 100 bis 2.000 mm reicht. Aufgrund des großen Maximal-Durchmessers muss die große Rohrschneidvorrichtung und das gesamte Stützrollensystem 1,25 m unter dem Bodenniveau versenkt werden. EGS stellt seine Rohre mit einem Durchmesser von über 900 mm mittels eines Blechbiegeprozesses her. Auf diese Weise hergestellte Rohre können leichte Rundheitsabweichungen aufweisen, die bei der Drehpositionierung des Rohres während des Schneidprozesses eine ungenaue Position der Schneidkonturen verursachen könnten. Die Maschine kann jedenfalls genaue Schneidergebnisse sicherstellen, indem sie die Rohre mit dem Laserscanner erfasst und die gemessenen Abweichungen anschließend kompensiert. Neben dem Plasmaschneiden ermöglicht die Maschine auch das Fasenschneiden von Rohren mit Autogen.
Schneiden von Trägern und Abweichungskompensation
Entlang des Schneidtischs ist ein Bereich zum Schneiden von Trägern bis zu einer Länge von 12 m und einer Steghöhe von 1.000 mm vorgesehen. Die Träger werden auf Auslegerstützen mit Spikes gelegt, unter denen sich ein Absaugkanal befindet. Die Maschine kann eine breite Palette von Trägertypen verarbeiten – U, L, IPE und HEA. Beim Schneidprozess bewegt sich das Portal inklusive Schneidwerkzeug entlang des statisch gelegten Profils, während der 5-Achsen-Rotatorkopf die Profiloberfläche von drei Seiten bearbeitet. Der spezielle „Pantograph“-Rotator kann den Plasmabrenner bis zu 120° neigen und ermöglicht so nicht nur das Schneiden von Löchern, sondern auch das Trennen von Profilen sowie das Schneiden von Konturen mit Fasen. Reale Träger können von den Standardmaßen abweichen und neigen ab bestimmten Längen zu Verdrehungen um die Längsachse. Um die geforderte Genauigkeit zu erreichen und Abweichungen zu kompensieren, wird jeder Träger vor dem eigentlichen Schneiden in dem Bereich des Schnitts eingescannt.
Um die Schweißnahtvorbereitung bei H-Trägern zu erleichtern, die bei EGS für die Herstellung von Plattformen für Kompressoranlagen verwendet werden, hat MicroStep zusätzliche kundenspezifische Makros für seine 3D-CAM-Software mCAM entwickelt. Dank der intelligenten Erstellung von Schneidplänen, dem Scannen und der umfassenden Steuerung der Schneidkopf-Bewegung ist es möglich, eine hohe Genauigkeit mit minimalem Bedarf an weiterer Oberflächenbearbeitung vor dem Schweißen zu erzielen.
mCAM trägt auch wesentlich zur Gesamteffizienz der Produktionsvorbereitung bei EGS bei. Es importiert und verarbeitet nicht nur komplexe 3D-Modelle von Teilen und Baugruppen auf einmal und zerlegt sie automatisch in schneidbare Formen, sondern lädt auch automatisch technologische Parameter von der angeschlossenen Schneidanlage, um entsprechende Schneidpläne zu generieren. Das ist besonders praktisch für die Bearbeitung von HEA- und IPE-Trägern, die unterschiedliche Steg- und Flanschdicken haben können und daher eine Anpassung der Schnittgeschwindigkeit an Übergängen erfordern. Dank der Kommunikation mit dem Steuerungssystem ist mCAM in der Lage, den Schneidplan für ein bestimmtes Halbprodukt automatisch zu generieren, einschließlich der Änderung der Schnittgeschwindigkeit beim Übergang zwischen verschiedenen Materialstärken in einem Träger.
Messbar mehr Geschwindigkeit in der Produktion
„Die Maschine ermöglicht es unserem Team, die Produktionszeit mit erhöhter Präzision in allen Phasen des Fertigungsprozesses zu optimieren", bewertet Roger Wachter. „Bei den Stutzenschnitten für Druckbehälter konnten wir die eigentliche Zeit für Layout, Schneiden und Schweißvorbereitung um mindestens 70 Prozent reduzieren. Ähnliche Ergebnisse zeigen sich beim Schneiden von I-Trägern für die Fertigung von Basis- und Subrahmen (Kompressor-/Treibermodule). Die 3D CAD/CAM-Software-Schnittstelle zwischen unserer Konstruktionsabteilung und der Schneidanlage eliminiert potenzielle Fehler, da keine menschliche Interaktion zwischen den Prozessen erforderlich ist", fügt Wachter hinzu.
ZITAT
„Bei den Stutzenschnitten für Druckbehälter konnten wir die eigentliche Zeit für Layout, Schneiden und Schweißvorbereitung um mindestens 70 Prozent reduzieren. Ähnliche Ergebnisse zeigen sich beim Schneiden von I-Trägern.“
Roger Wachter,
General Manager | Euro Gas Systems
MicroStep zählt zu den weltweit führenden Herstellern CNC-gesteuerter Schneidsysteme. Das Unternehmen entwickelt und produziert Plasma-, Autogen-, Laser- und Wasserstrahl-Schneidanlagen – von kleinen CNC-Maschinen für Schulen und Werkstätten bis hin zu maßgeschneiderten Fertigungsstraßen für Schiffswerften, Stahlcenter oder die Automobil- und Luftfahrtindustrie. Zudem bietet MicroStep vielfach erprobte Automationslösungen: Vom Materialhandling rund um die Schneidanlage bis hin zur Kommissionierung und Sortierung geschnittener Teile.
Die international tätige MicroStep Gruppe wurde Anfang der 1990er-Jahre in der slowakischen Hauptstadt Bratislava gegründet. Zu ihr gehört die MicroStep Europa GmbH, die speziell für Kunden aus dem deutschsprachigen Raum Beratung, Planung, Finanzierung, Schulung und Support zu allen MicroStep-Produkten bietet. Darüber hinaus entwickelt und vertreibt die MicroStep Europa GmbH weltweit auch eigenständige Produkte & Dienstleistungen.
Am Firmensitz im bayerischen Bad Wörishofen betreibt MicroStep Europa das CompetenceCenter Süd, an der Niederlassung in Dorsten (NRW) das CompetenceCenter Nord. Ständig stehen in den beiden Schulungs- und Vorführzentren modernste Schneidlösungen bereit.
Darüber hinaus ist MicroStep in Deutschland noch mit zwei Stützpunkten in Kiel (Schleswig-Holstein) und Berlin vertreten. Für Österreich unterhält MicroStep einen Stützpunkt bei Wien (in Bratislava, Slowakei) und in der Schweiz bei Bern (beim MicroStep-Partner LWB WeldTech AG in Wünnewil).
Mehr erfahren: www.microstep.com
MicroStep Europa GmbH
Messerschmittstraße 10
86825 Bad Wörishofen
Telefon: +49 (8247) 96294-00
Telefax: +49 (8247) 96294-09
http://microstep.com
Marketing & Kommunikation
Telefon: +49 (8247) 96294-73
Fax: +49 (8247) 96294-79
E-Mail: melanie.soehnel@microstep-europa.de

