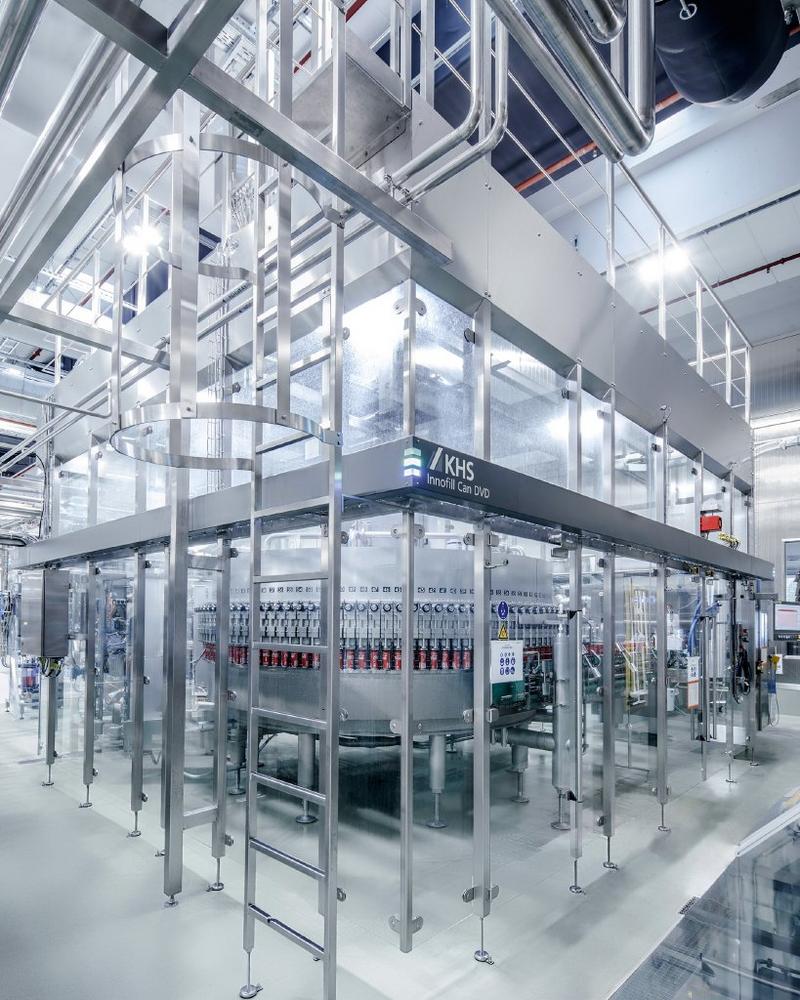
Bleibt in der Familie
Sein Beruf bei Coca-Cola HBC im österreichischen Edelstal wird Patrick Redl quasi in die Wiege gelegt: Vor vier Jahren folgt er dem Vorbild seines Vaters, der 37 Jahre lang und zuletzt als Werksleiter bei „Römerquelle“ angestellt war – einem Mineralbrunnen, der 2003 von dem weltweit drittgrößten Abfüller der Marke Coca-Cola übernommen wurde. Anders als der Senior konnte Redl junior zwar nicht mehr in Römerquelle schwimmen lernen: „Das mit dem Mineralwasser gefüllte Schwimmbad neben der Fabrik wurde leider schon 1971 stillgelegt“, sagt er. „Aber trotzdem fühle ich mich, als wäre ich im Werk aufgewachsen.“ So viel Zeit hat er in seiner Kindheit und Jugend dort damit verbracht, seinem Vater über die Schulter zu schauen.
Idyllischer Standort
Edelstal, nur einen Steinwurf von der slowakischen Grenze und Hauptstadt Bratislava entfernt, ist ein idyllischer 800-Seelen-Ort im nördlichen Burgenland. In das Dorf, das malerisch zwischen zwei Hügeln eingebettet liegt, verirrt sich kaum jemals ein Tourist. Unmittelbar am Ortseingang befindet sich hier das Produktions- und Logistikzentrum von Coca-Cola HBC Österreich, dessen Grundfläche ungefähr der des ganzen Ortes entspricht. Um sich ein Bild von der schieren Größe des Werks zu machen, muss man sich nur vergegenwärtigen, dass auf den Hallendächern eine der größten Photovoltaikanlagen ganz Österreichs installiert ist.
Seit den Anfängen in den Vierzigern und dem Übergang zum industriellen Abfüllen der Römerquelle in den Sechzigerjahren hat sich viel getan: Nach der Übernahme wird der Betrieb innerhalb von nur zehn Jahren sukzessive ausgebaut und modernisiert, bis er schließlich das bisherige Coca-Cola-Werk in Wien sowie eine Fabrik in der benachbarten Slowakei ablöst: Seit 2013 werden in dem hochmodernen Abfüll- und Logistikzentrum in Edelstal fast alle Softdrinks für den österreichischen Markt abgefüllt und von hier aus landesweit ausgeliefert. Heute gibt es in Edelstal insgesamt elf Produktionslinien: Auf drei davon wird Mineralwasser abgefüllt – eine klassische PET-Linie, eine Glaslinie sowie eine PET-UltraClean-Linie für die Abfüllung sensitiver Produkte. Auf weiteren sieben Linien – dreimal PET, einmal Glas, einmal Bag-in-Box und zweimal Keg – werden Softdrinks, Energydrinks sowie Säfte und Sirup verarbeitet. Jüngster Meilenstein ist die im vergangenen Jahr durch KHS in Betrieb genommene erste Dosenlinie in der Geschichte des Standorts.
„So wie Dosen für uns eine ganz neue Kategorie von Primärverpackungen sind, ist Metall ein Material, das wir bisher nicht eingesetzt haben“, sagt Patrick Redl. „Wir haben bei der Gestaltung der Linie ganz besonderen Wert darauf gelegt, dass die Technologie in jeder Hinsicht zukunftsfähig ist und uns mit Blick auf künftige Markttrends und Produktinnovationen größtmögliche Flexibilität bietet.“ Schon bei der Entwicklung des Layouts der neuen Anlage bringt KHS viele konstruktive Vorschläge ein, wie diese später mit geringem Aufwand ergänzt werden kann – etwa durch einen Pasteur, eine zusätzliche Verpackungsmaschine oder die Option, Halbpaletten zu verarbeiten. „Nicht umsonst erhielt die Linie bei uns sehr schnell den Spitznamen „Iron Unicorn“, das eiserne Einhorn. Damit wollten wir ausdrücken, dass sie so etwas wie die sprichwörtliche eierlegende Wollmilchsau ist. Passend dazu haben wir unseren Produktionsleiter „Iron Man“ genannt“, sagt Redl.
Anspruchsvolles Timing
Die erste von mehreren Herausforderungen ist der enge Zeitrahmen: „Im Oktober 2019 wurden wir damit beauftragt, eine Dosenanlage zu installieren und bis Juni 2020 in Betrieb zu nehmen“, erinnert sich der Werksleiter. „Das war ein anspruchsvolles Timing – schon allein angesichts der behördlichen Genehmigungen: Nur drei Tage nach dem Go haben wir das Projekt der Landesregierung vorgestellt, damit dort die notwendigen Ressourcen geblockt werden konnten.“
Komplex ist das Projekt vor allem deshalb, weil es das gesamte Werk betrifft: Die neue Linie soll in einem Bereich aufgestellt werden, wo sich bisher das Rohmateriallager befindet. Dieses soll dafür dorthin umziehen, wo bisher die Streckblasanlagen stehen. Und für jene wiederum muss erst ein Palettierer Platz machen. „Das war wie eine Kettenreaktion und erforderte eine extrem genaue Planung“, erklärt Redl. „Bereits im November begann die Übersiedelung. Das Lager hat uns bis in den Mai beschäftigt, weil an seinem neuen Standort weniger Fläche zur Verfügung stand. Hier kam deshalb ein verfahrbares Regalsystem zum Einsatz, das man sonst aus Aktenarchiven kennt.“
Trotz Corona-Pandemie: herausfordernden Zeitplan eingehalten
Bevor KHS die Maschinen für die neue Dosenanlage anliefern konnte, musste nun die alte Lagerhalle hergerichtet werden – vom komplett neuen Boden über die Verlegung von Rohren und Leitungen bis hin zur Installation der Lüftungs- und Lichtanlagen. „Das sind nur einige der unzähligen Vorbereitungen, die nötig sind, bevor es losgehen kann. Letztlich hat aber alles funktioniert wie ein Schweizer Uhrwerk – wenn ich als Österreicher das feststellen darf“, meint Redl. Und das, obwohl sich zwischenzeitlich eine weitere Komplikation ergeben hat: „Wir fühlten uns auf einem guten Weg, den Termin im Juni einhalten zu können“, blickt Redl zurück. „Mit einem Auge haben wir natürlich verfolgt, was sich seit Januar in China zusammenbraute, hofften aber, dass es an uns irgendwie vorbeigeht. Bekanntlich schwappte Corona dann doch nach Europa und erreichte Österreich – eine Situation, die uns ganz sicher nicht geholfen hat. Dennoch haben wir keine Minute daran gezweifelt, dass wir unseren Zeitplan einhalten können – das waren ein unglaublicher Spirit und eine große Agilität. Als wir es tatsächlich geschafft hatten, alle Vorbereitungen zum Stichtag pünktlich abzuschließen, war selbst KHS ein bisschen überrascht, glaube ich.“
Der Schutz der Mitarbeiter sowie des KHS-Installationsteams und aller weiteren in Edelstal beschäftigten Subunternehmer hat vom ersten Augenblick an oberste Priorität. Die damit verbundenen Restriktionen machen die Arbeit natürlich nicht leichter: Abstände müssen eingehalten, Menschen voneinander separiert werden. „Die Unternehmenszentrale hat uns bei der Schaffung einer sicheren Umgebung sehr unterstützt – nicht zuletzt durch die Lieferung von Masken, die anfangs bei uns noch Mangelware waren. Wir haben immer wieder Lösungen gefunden“, sagt Redl. Man schafft eine sichere Umgebung, in der sich alle Beteiligten voll auf die Installation der Linie konzentrieren können. Dafür, dass es während des Projekts keinen einzigen Covid-19-Fall im Team gab, können sich am Ende alle auf die Schulter klopfen.
Letztendlich konnte der Termin für die Getränkeproduktion gegen alle Widrigkeiten eingehalten werden. Das ist auch ein Verdienst der eingeschworenen Mannschaft aus eigenen und KHS-Mitarbeitern, findet Redl: „Da ist Tag für Tag wirklich grandiose Arbeit geleistet worden. Am wichtigsten war für mich die permanente Abstimmung, das Gefühl, von der Planung über die Vorbereitung bis hin zur Aufstellung Schulter an Schulter zusammenzustehen – bis heute. Ich jedenfalls bin sehr stolz darauf, dass wir das unter diesen Rahmenbedingungen geschafft haben.“
Strategischer Schlüssellieferant
Insgesamt hat Coca-Cola HBC 2020 in sechs Ländern von KHS jeweils eine neue Dosenlinie installieren und in Betrieb nehmen lassen. Grund für die Investition war einerseits die gestiegene Nachfrage nach den Aluminiumbehältern: „Dosen werden immer beliebter, vor allem in Europa“, erklärt Theodoros Kappatos, Group Engineering Manager von Coca-Cola HBC. „Als ein führender Getränkehersteller in vielen europäischen Märkten müssen wir uns natürlich auf diesen Trend einstellen. Außerdem konnten wir mit unserer neuen Dosenlinie auch eine Strategie entwickeln, um aromatisiertes Wasser der Marke Römerquelle in Aluminiumdosen anzubieten.“ Andererseits sind die Neuanschaffungen Teil der Supply-Chain-Strategie des Abfüllers. Eines von deren Zielen ist die Modernisierung von Produktionslinien, insbesondere indem veraltete Anlagen durch neue, effizientere, verbrauchsärmere und leistungsfähigere Technologie ersetzt werden.
Mit KHS verbindet Coca-Cola HBC eine langjährige und vertrauensvolle Zusammenarbeit: „Wir haben KHS diesen Auftrag erteilt, weil das Unternehmen für uns ein großartiger Partner ist“, betont Kappatos. „Das gilt nicht nur hinsichtlich dieses Behälterformats, sondern für unser gesamtes Anlagenportfolio. Erst kürzlich haben wir zum Beispiel gemeinsam eine PET-Linie in unserem Werk in Kiew in Betrieb genommen. Wir betrachten KHS als einen strategischen Schlüssellieferanten an unserer Seite: Ein Partner, der unseren Anspruch an effiziente und qualitativ hochwertige Maschinen und Anlagen versteht und einlöst. Das wiederum versetzt uns in die Lage, die Bedürfnisse unserer Kunden und der Verbraucher erfüllen zu können. Besonders schätzen wir, dass der Fokus unserer Zusammenarbeit nicht nur auf innovativen Konzepten liegt, sondern dass unkonventionelle Ideen eingebracht werden. Auf deren Basis erzielen wir beispielsweise eine bessere Funktionalität sowie eine kostengünstigere und einfachere Wartung.“
Begeistert ist auch Patrick Redl in Edelstal: Nicht nur die hohe Geschwindigkeit der Linie hat es ihm angetan, die bis zu 90.000 Dosen in der Stunde füllt: „Das haut mich um! Die läuft doppelt so schnell wie die zweitschnellste unserer Linien!“ Auch das Tempo, mit dem die neue Anlage im Vergleich zu allen bisherigen auf Leistung war, hat ihn überrascht. Besonders glücklich ist er unter anderem mit einer neuen Technologie, die jeweils sechs Dosen mit dem innovativen KeelClip™ aus Pappe zu Sixpacks zusammenfügt. Die Reduzierung von Kunststoffen in Sekundärverpackungen ist Teil der „World Without Waste“-Selbstverpflichtung von Coca-Cola HBC. „Wir waren einer der ersten weltweit, die diese ganz neuen Maschinen ans Laufen gebracht haben“, stellt er fest. „Geschafft haben wir das mit Hilfe von modernsten digitalen Lösungen wie VR-Brillen – schließlich durften die Techniker des US-amerikanischen Herstellers nicht ausreisen.“ Wertvolle Unterstützung sei hier von KHS gekommen, die viel Know-how in die Integration der Maschine in der Linie eingebracht haben – ganz wie man das in einer solchen Partnerschaft erwarten darf.
Wenn Redl in seiner Freizeit seinen Vater besucht und sich zum Essen an den Familientisch setzt, müsse man sich das immer noch ein bisschen vorstellen wie ein Meeting, sagt der Junior am Ende unseres Gesprächs. Aber bei aller Erfahrung, die sein Vorgänger ihm voraushaben mag, könne dieser ihm eins jedenfalls nicht nehmen: „Der Werksleiter zu sein, der als erster die Römerquelle in Dosen gebracht hat, ist schon etwas einmaliges“, stellt er lachend fest.
Überblick: Großprojekt
Insgesamt sechs Dosenlinien hat Coca-Cola HBC im Jahr 2020 bei KHS bezogen. Bestellt wurde ein Paket sechs ähnlicher Linien – mit lokalen Unterschieden hinsichtlich Kapazität, Verpackung und Einzelmaschinen:
- Ikeja (Nigeria) bis zu 45.000 Dosen pro Stunde
- Lisburn (Nordirland) bis zu 45.000 Dosen pro Stunde
- Edelstal (Österreich) bis zu 90.000 Dosen pro Stunde
- Novosibirsk (Russland) bis zu 90.000 Dosen pro Stunde
- Niepołomice (Polen) bis zu 90.000 Dosen pro Stunde
- Kiew (Ukraine) bis zu 90.000 Dosen pro Stunde
Die KHS Gruppe ist einer der weltweit führenden Hersteller von Abfüll- und Verpackungsanlagen in den Bereichen Getränke und flüssige Lebensmittel. Zur Unternehmensgruppe zählen neben der Muttergesellschaft (KHS GmbH) diverse ausländische Tochtergesellschaften mit Produktionsstandorten in Ahmedabad (Indien), Waukesha (USA), Zinacantepec (Mexiko), São Paulo (Brasilien) und Kunshan (China). Hinzu kommen zahlreiche internationale Verkaufs- und Servicebüros. Am Stammsitz in Dortmund sowie in ihren weiteren Werken in Bad Kreuznach, Kleve, Worms und Hamburg stellt die KHS moderne Abfüll- und Verpackungsanlagen für den Hochleistungsbereich her. Die KHS Gruppe ist eine 100-prozentige Tochtergesellschaft der im SDAX notierten Salzgitter AG. 2020 realisierte die Gruppe mit 5.085 Mitarbeitern einen Umsatz von rund 1,130 Milliarden Euro.
KHS GmbH
Juchostr. 20
44143 Dortmund
Telefon: +49 (231) 569-0
Telefax: +49 (231) 569-1541
http://www.khs.com
Presse- und Öffentlichkeitsarbeit
Telefon: +49 (251) 625561-243
E-Mail: deppe@sputnik-agentur.de

