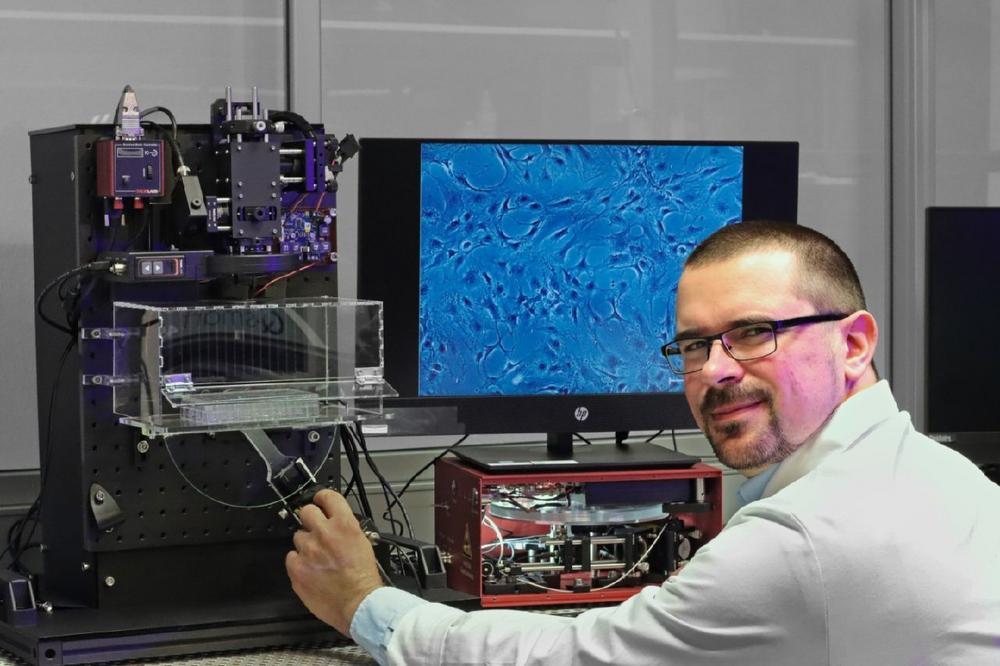
New light source: A million times brighter than the sun
In his PhD thesis, Dr. Tobias Baselt focused on enhancing the optical performance of white-light lasers in metrology. The aim was to minimize costs, time and errors, for example in chip production or microbiology. To this end, the scientist investigated the application of white-light laser sources in two different measurement processes. The result was a new light source – a million times brighter than the sun and can be easily integrated into manufacturing processes – without having to stop them or segregate samples. Today, Baselt heads the Optical Fiber Technology group at Fraunhofer AZOM and is a research associate at the Faculty of Physical Engineering at WHZ. ”In my PhD thesis, I researched the application of specially developed laser sources with white laser light, which are particularly high-performing compared to the current state-of-the art and therefore very promising for microbiological and industrial measurement methods,” he explains.
Quality control in the semiconductor industry and microbiology
Particularly in high-cost manufacturing processes in the semiconductor industry, such as chip production, significant potential savings could thus be achieved. Baselt demonstrated that the white-light laser process can perform quality control of semiconductor elements more quickly. For example, the intensity of the light source can be used to characterize the surface profile, deeper structures and even the reverse side of microchips in a single process. Microbiology could also benefit from the new light source, for example in cell culture studies. In this process, the white-light laser, also known as a supercontinuum source in technical jargon, is focused on the cell for a brief moment. The intensity of this light source permits the imaging of the smallest cell structures without destroying them. With this measurement method, cells can be monitored in real time, allowing early detection of cell changes as well as cell damage. Whereas it was previously only possible to record them at fixed times, Tobias Baselt’s solution makes it possible to record their states non-invasively. This allows close monitoring of the drug impacts, particularly in bioreactors or in toxicity tests. In the next steps, the laboratory results will be further investigated and developed for integration into industrial processes.
About the scientist
In the course of his PhD thesis on “Selected methods for optimization of supercontinuum generation in optical metrology”, Dr. Tobias Baselt published four peer-reviewed papers, three of which he was first author. He presented his results at international conferences in various countries. In addition, he worked on a total of six patents during this time, four of which have already been granted. Since 2015, Mr. Baselt has headed the “Optical Fiber Technologies” group at Fraunhofer AZOM. As a scientist, he has already been researching at Westsächsische Hochschule Zwickau (WHZ) since 2006. He completed the cooperative PhD with WHZ and TU Dresden as “Dr.-Ing.” in September 2021.
About the Fraunhofer Application Center for Optical Metrology and Surface Technologies (AZOM)
The Fraunhofer Institute for Material and Beam Technology IWS operates the Fraunhofer Application Center for Optical Metrology and Surface Technologies (AZOM) in cooperation with Westsächsische Hochschule Zwickau (WHZ). Here, scientists research and develop the latest approaches in optical metrology, image processing, process control and surface characterization. They focus on transferring research results quickly and directly into application-specific solutions for industrial processes. Fraunhofer AZOM provides an interface between applied science and industry in the fields of medical technology, automotive engineering, mechanical engineering and semiconductor technology.
The Fraunhofer Institute for Material and Beam Technology IWS Dresden develops complex system solutions in materials and laser technology. We define ourselves as idea drivers developing customized solutions based on laser applications, functionalized surfaces as well as material and process innovations – from easy-to-integrate custom solutions to cost-efficient solutions for small and medium-sized enterprises to industry-ready one-stop solutions. Our research focuses on aerospace, energy and environmental technology, automotive, medical and mechanical engineering, toolmaking, electrical engineering and microelectronics, and photonics and optics sectors. In our five future and innovation fields of battery technology, hydrogen technology, surface functionalization, photonic production systems and additive manufacturing, we are already creating the basis today for the technological answers of tomorrow.
Fraunhofer-Institut für Werkstoff- und Strahltechnik IWS
Winterbergstraße 28
01277 Dresden
Telefon: +49 (351) 83391-0
Telefax: +49 (351) 83391-3300
http://www.iws.fraunhofer.de
Head of Optical Fiber Technology
Telefon: +49 (375) 536-1970
E-Mail: tobias.baselt@iws.fraunhofer.de
Leiter Unternehmenskommunikation
Telefon: +49 (351) 83391-3614
Fax: +49 (351) 83391-3300
E-Mail: markus.forytta@iws.fraunhofer.de
