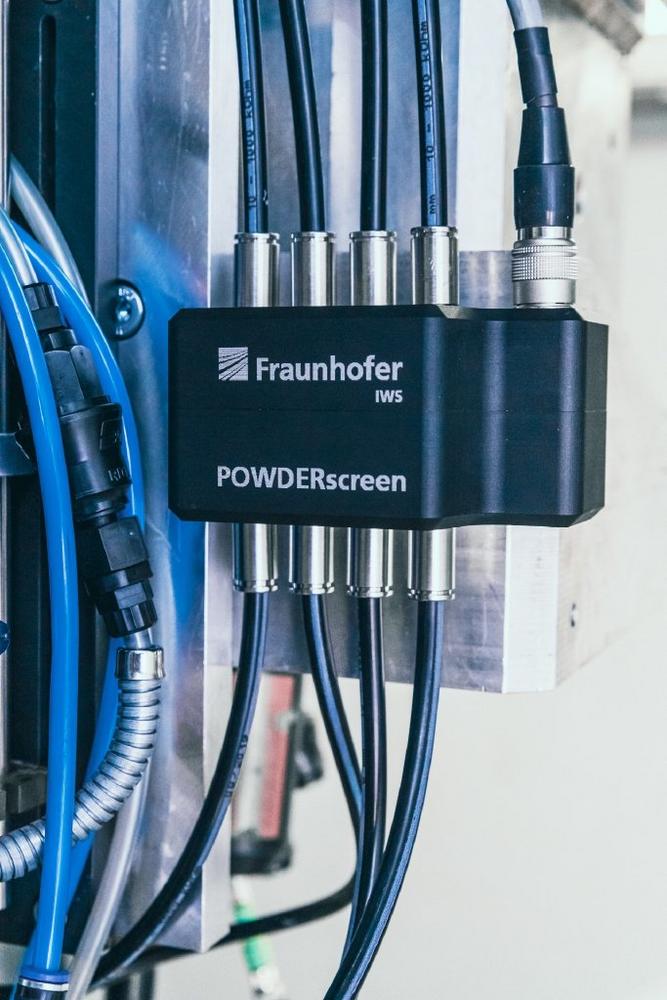
POWDERscreen monitors streams of powder into the laser melt
POWDERscreen is designed for laser cladding. In this additive manufacturing, coating and repair process, special nozzles deliver concentrated streams of metal powder precisely into the focus of a laser beam. This fuses the powder onto the surface of the workpiece in order to create complex 3D structures from this melt. In the future, the powder flow meter will make it possible to measure exactly which metals flow in what quantity into the laser focus. This approach can reduce the costs of powder-based laser cladding, improve the quality of the components produced and make the entire production process precisely repeatable – a particularly important requirement in high-tech industry.
Important step towards a controlled manufacturing process
“So far, powder-based laser cladding still falls short of its potential,” Rico Hemschik assesses. The engineer at Fraunhofer IWS has developed POWDERscreen. “With the powder flow meter, we are taking a big step towards a more efficient, controlled and automated additive manufacturing process.” To make this possible, the system combines modern sensor technology with special software, a screen, and interfaces for data transfer. Photo sensors count the particles in the powder stream, and the software uses them to calculate the feed rates. The screen displays the processed data to the machine operator.
A particular advantage is the universal applicability: POWDERscreen can be mounted on any process head for powder laser cladding. One application example in which it shows its strengths particularly well is the COAXquattro nozzle. This process head was developed at Fraunhofer IWS to feed up to eight different powders or wires in separate channels into the laser focus to produce in-situ alloys. Since the COAXquattro supports up to 30 grams per second per channel, significant powder rates can be achieved. Because of the large feed rates, the combination of COAXquattro and POWDERscreen is particularly suitable for high-performance processes in which large and complex components have to be produced, coated or repaired with high quality, reproducibility and speed.
POWDERscreen can also be combined with other process monitoring systems developed by Fraunhofer IWS. These include the Emaqs camera for process control, the COAXjay sensor box or the LIsec measurement system for powder cone geometry. Via its interfaces, POWDERscreen can be integrated together with these devices into modern industrial environments or solutions for the Industrial Internet of Things (IIoT). For example, analog data output is possible via a voltage interface, via the IIoT protocol “Message Queuing Telemetry Transport” (MQTT) or data transfer via software.
Possible automatic genesis of “digital twins”
In the future, such combined process monitoring systems should also independently generate digital twins of additively produced components. The information about where the laser melted, alloyed and shaped which powder and in what quantity can in principle also be automatically merged into a virtual computer model. Using conventional methods, it would be difficult or impossible to accurately model such local alloy changes within a component.
The researchers at Fraunhofer IWS see great application potential for POWDERscreen in the aerospace industry, among others. There, for example, the system can be used to reproduce and repair intricately shaped turbine blades with additive processes in consistently high quality. The same applies to stamping tools in automotive manufacturing or prototype production across almost all sectors of industry.
If machine operators in the future no longer have to set up powder-based laser cladding systems "freehand" and with numerous trials, but on the basis of precisely recorded and repeatable process parameters, the advantages are obvious: The run-in curve is shortened, the reject rate at the start of a small series is reduced. In addition, the processes become more efficient and reproducible in high quality. Last but not least, they can be documented automatically in the future – which in turn can prove important for later warranty claims.
High Entropy Alloys (HEA) and Additive Manufacturing at the German Hygiene Ministry Dresden
In order to explore new application scenarios for the POWDERscreen, Fraunhofer IWS will present the so far unrivaled system from May 11 to 13, 2022 during the “3rd Symposium on Materials and Additive Manufacturing” at the German Hygiene Museum.
During this conference organized by the German Society for Materials Science e. V. (DGM), the institute will host the symposium “High Entropy Alloys: Potential for industrial applications” on May 12, 2022. The focus will be on the opportunities and challenges of industrializing novel, so-called high entropy alloys for potential users.
Further information:
- HEA-Symposium: https://s.fhg.de/hea-2022
- Symposium: https://dgm.de/additive/2022 (German)
- Deutsche Gesellschaft für Materialkunde e. V.: https://dgm.de
Materials and Lasers – Competence with a System: The Fraunhofer Institute for Material and Beam Technology IWS develops complex system solutions in materials and laser technology. We define ourselves as idea drivers developing customized solutions based on laser applications, functionalized surfaces as well as material and process innovations – from easy-to-integrate custom solutions to cost-efficient solutions for small and medium-sized enterprises to industry-ready one-stop solutions. Our research focuses on aerospace, energy and environmental technology, automotive, medical and mechanical engineering, toolmaking, electrical engineering and microelectronics, and photonics and optics sectors. In our five future and innovation fields of battery technology, hydrogen technology, surface functionalization, photonic production systems and additive manufacturing, we are already creating the basis today for the technological answers of tomorrow.
Fraunhofer-Institut für Werkstoff- und Strahltechnik IWS
Winterbergstraße 28
01277 Dresden
Telefon: +49 (351) 83391-0
Telefax: +49 (351) 83391-3300
http://www.iws.fraunhofer.de
Division Manager Additive Manufacturing
Telefon: +49 (351) 83391-3296
Head of Corporate Communications
Telefon: +49 (351) 83391-3614
Fax: +49 (351) 83391-3300
E-Mail: markus.forytta@iws.fraunhofer.de