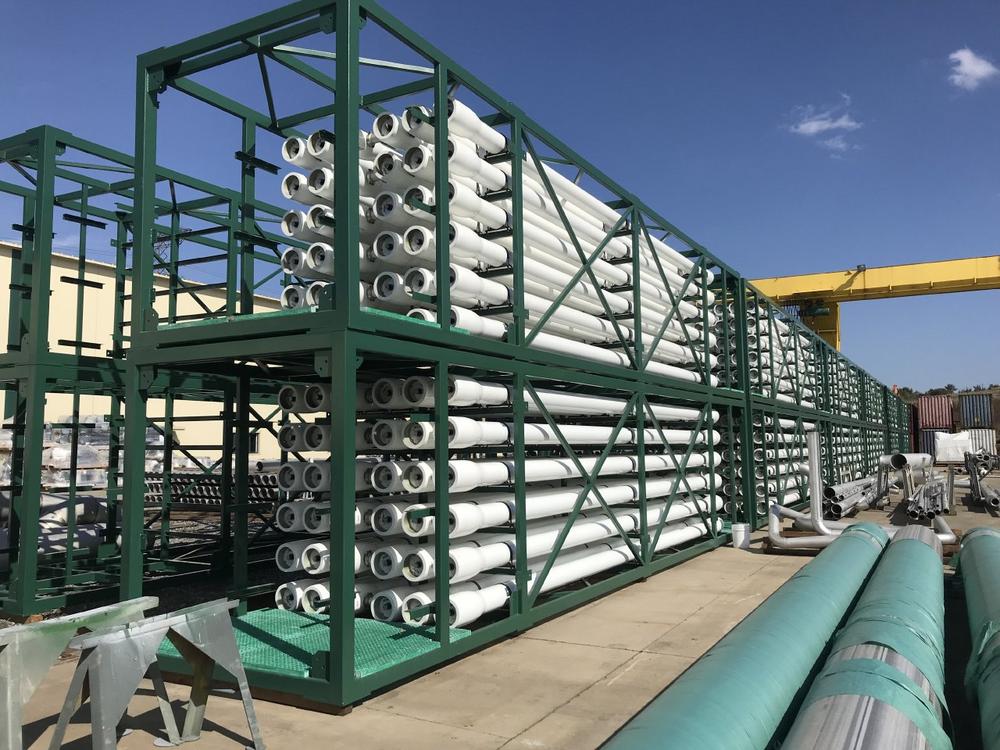
200 000 m3 of drinking water per year
The drinking water supply has been a major challenge for Israel for years. The country’s natural water resources are scarce – water consumption is increasing.
With the help of five large seawater desalination plants, Israel wants to counteract this trend in the future. For the construction of the latest plant south of Tel Aviv, BUTTING is supplying entire modules and connecting pipelines as a one-stop shop.
Containerisable solutions
A total of 192 modules are manufactured in our factory in Tieling, delivered to Israel and assembled. The almost five kilometres of piping components in the dimensions ½" to 24", weighing 200 metric tons, as well as the 2 800 stainless steel fittings weighing almost 100 metric tons, mainly made of superduplex, were 100 per cent prefabricated in Tieling. They were then non-destructively tested and mounted in the base frames in carbon-manganese steel.
3 500 high-pressure filters had to be installed, aligned and inserted, and a good 900 control valves, flow meters, etc. had to be installed and wired to the more than 390 control cabinets.
“With us, customers get a complete solution,” explains Jens Ellermann, Managing Director of BUTTING in China. “We not only assemble the piping components in the base frame, but also all the equipment provided, such as vessels, pumps, apparatus, other components, fittings, expansion joints and electrical field devices, and insulate items at the customer’s request.”
The modules are used as a central component in the desalination and treatment process of the plant and have to withstand heavy stresses very reliably in an extremely corrosive environment. At the customer’s request, an elaborate three-coat paint finish was therefore applied to all modules. Furthermore, high demands with regard to dimensional accuracy are to be met to ensure that the materials arrive on site ready for installation, with an absolutely precise fit.
Jens Ellermann reports that “the advantages of BUTTING prefabrication pay off here: more than 95 per cent of the welding seams are produced in-house by BUTTING. This shop welding and the pickling of whole components ensure the required seam and surface quality. In addition, non-destructive tests are already carried out on BUTTING’s premises. This means that pressure tests, dye-penetrant tests and X-ray testing are not required on the construction site. The result is higher quality and shorter throughput times for the benefit of our customer.”
The modules and pipelines are called off depending on the construction progress. This just-in-time delivery allows BUTTING to ensure clear operational planning that meets the customer’s requirements.
Commissioning of the plant is planned for 2023. Then it will get noisy in the new halls on the industrial site near the Mediterranean coast south of Tel Aviv. Large pumps will pump salt water at high pressure from the Mediterranean Sea through 5 kilometres of pipelines at a depth of 21 metres into dozens of basins. Each pressure vessel is equipped with membranes that filter out salt and minerals to produce drinking water.
The physical process is called reverse osmosis. Every year, 200 million m3 of seawater are to be treated in this way to become drinking water.
BUTTING – more than pipes – for a better quality of life
BUTTING Gruppe
Gifhorner Straße 59
29379 Knesebeck
Telefon: +49 (5834) 50-0
Telefax: +49 (5834) 50-320
http://www.butting.com
Marketing and communications
Telefon: +49 (5834) 50-7091
E-Mail: Imke.Elbadaoui@butting.de

