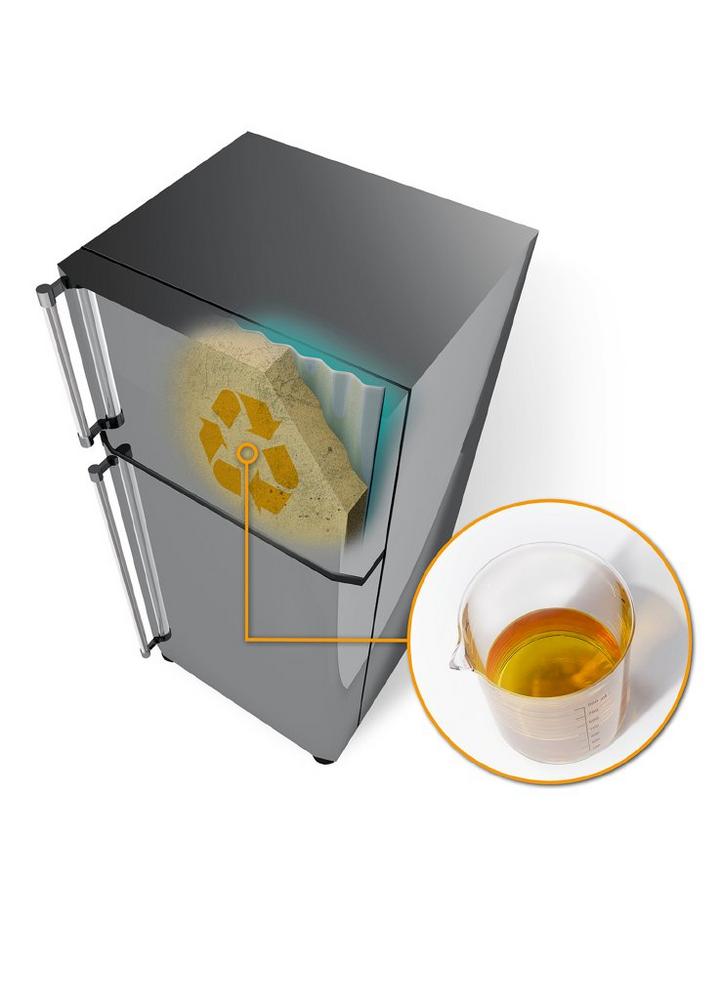
Go! Create something new from old PUR and close the material loop for PUR rigid foams
Refrigerators have a long lifespan. To ensure energy efficiency and as little CO2 emissions as possible, manufacturers of almost all appliances all around the world rely on the insulation performance of polyurethane. PUR is an energy saver during its service life. But what happens at the end of the life cycle when the refrigerators and thus the PUR rigid foam have done their job?
After disposal, as prescribed by the EU in Directive 2012/19/EU on waste electrical and electronic equipment (WEEE), the rigid foam ends up as regrind, which up until now has mainly been used for energy purposes. According to PlasticsEurope, this process recovers about 30 per cent of the energy used in the production of PUR, but the carbon is not retained in the material cycle. The four partners will change that by using a new chemical recycling process known as depolymerization to obtain a recycled polyol. This polyol is to be used in the production of PUR materials in order to close the material cycle.
This innovative process is particularly challenging, because it has to be very robust in order to reliably convert post-consumer waste with high levels of foreign substances into a high-quality recycled polyol. The progress made by the four partners is promising. The initial trials have already produced positive results.
To date, processes for the chemical recycling of PUR have mainly focused on industrial waste, usually from production. This industrial waste is characterized by a high degree of purity, which significantly facilitates recycling. The recycling stream originating from post-consumer waste is much more complex to handle, as it is heavily contaminated with foreign substances such as other types of plastics and metals.
For the process to make it from the lab to everyday life: Few partners, high efficiency
What works in pilot projects should ultimately be implemented on an industrial scale. Therefore, new technologies are needed, and all the players in the recycling chain – from the dismantling of the refrigerator to the use of recycled polyol in the production process – must work together efficiently. It is also important that every stage of the recycling process is assessed ecologically and economically. And this is precisely the approach taken by KraussMaffei, RAMPF, REMONDIS, and BASF. The goal is to develop an industrial process that delivers high-quality recycled polyols that are comparable to polyols obtained from primary fossil raw materials.
BASF Polyurethanes GmbH, Lemförde, is responsible for the chemical testing and qualitative evaluation of the recycled material obtained. For the raw material supplier and system provider in the field of polyurethanes, it is an important concern to work in partnership on end-of-life solutions. Joerg Krogmann, Technical Development at BASF, explains his view of the project: “The chemical recycling process of PUR waste from refrigerator recycling that will be developed during this collaboration must be economically and ecologically sustainable, while also meeting BASF’s high product quality requirements.”
First step: collection and processing of the waste material
A basic prerequisite for this recycling project is that the collection and dismantling of the old refrigerators and freezers run smoothly. This is one of the reasons why REMONDIS Electrorecycling GmbH, Lünen, is part of the team. “A basic prerequisite for an innovative waste equipment recycling route is that the waste management industry makes the appropriate waste material available to the other players in the recycling chain according to the correct specifications and in industrial quantities. And that is what we are working on. We are the first step in the sustainable supply of raw materials,” says Sebastian Schormann, ear sales manager and authorized signatory at REMONDIS.
RAMPF Eco Solutions GmbH, Pirmasens, is contributing its experience in the chemical recycling of polyurethane and PET residues to the project. “We want to establish innovative process technologies that are better able to deal with increased levels of foreign substances in post-consumer materials,” says Michael Kugler, plant manager and authorized signatory at RAMPF Eco Solutions, describing his interest in the collaboration.
As a machine and systems manufacturer, KraussMaffei not only focuses on the production of plastics, but also on their recycling and sustainable use at the end of their life cycle. In the collaboration, KraussMaffei is responsible for the development of the technology and of efficient overall technical concepts for plastics plant engineering. Sebastian Schmidhuber, trend scouting manager at KraussMaffei Technologies GmbH, Munich, explains: “Together with our partners, we want to advance technologies for the chemical recycling of polyurethane materials in this project. Recycling plastics has a great future – and it requires the right technologies and machines.”
RAMPF Eco Solutions based in Pirmasens, Germany, is an expert in chemical solutions for the manufacture of high-quality recycled polyols.
Core competence is the manufacture of polyols from waste materials of polyurethane (PU) producers.
Furthermore, the company has developed chemical processes that enables PET / PSA, other polyesters (PLA, PC, PHB), and renewable or bio-based raw materials such as vegetable oils to be used as sources of raw materials for the manufacture of recycled polyols.
RAMPF Eco Solutions also designs and builds customized multifunctional plants for customers who wish to manufacture recycled polyols based on PU residues, PET / PSA, polyesters, and biomonomers.
RAMPF Holding GmbH & Co. KG
Albstraße 37
72661 Grafenberg
Telefon: +49 (7123) 9342-0
http://www.rampf-group.com
Pressereferent
Telefon: +49 (7123) 9342-0
E-Mail: pr@rampf-group.com
