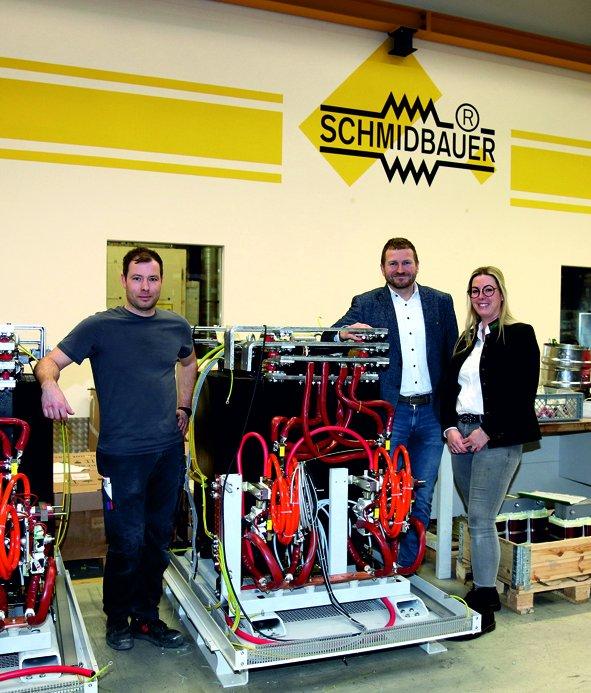
Water-cooled transformers for up to 2,700 kVA
Whether on rail vehicles, electric excavators or in control cabinets: installation space is a scarce and expensive commodity that even cannot be increased in retrofitting. In order to make transformers as compact as possible, Schmidbauer uses potential-free water cooling with operating pressures of up to 6 bar. Since one litre of water can absorb as much waste heat as 4 m³ of cooling air, the entire system can be set up in a very space-saving and also extremely maintenance-friendly manner: Fans, wind tunnels and filters can be completely dispensed off – and with them the maintenance efforts required to clean them regularly.
With this Schmidbauer system, the waste heat is transferred to the cooling water and can be used energetically – in contrast to forced cooling, where heat energy simply escapes. The energy balance is even worse if the waste heat is released into operating rooms and then has to be air-conditioned out in an energy-intensive process. Accordingly, Schmidbauer mainly equips larger isolating or autotransformers according to IEC/DIN EN61558-2-13 or IEC/DIN EN61558-2-4 in the power range between 20 and 2,700 kVA with this innovative technology. The standard input voltage is 3 x 400 V at 50 or 60 Hz. Customer-specific designs for other voltages and/or frequencies can be put into reality at any time.
For its water cooling, Schmidbauer integrates hoses made of a special plastic into the windings. The heat from technically unavoidable hot spots in the transformer is dissipated by integrated cooling plates. The Schmidbauer system allows water pressures of up to 6 bar. Quick couplings facilitate uncomplicated integration into a cooling network with power electronics, mains filters, drives or other heat sources. The number of cooling circuits, the inlet pressure and the water temperature in the supply and return lines depend on the operating mode of the transformer or are adapted to the requirements of the load. In this way, as much heat loss as possible is dissipated in a targeted manner – and becomes directly usable, e.g., for low-temperature heating systems.
For physical reasons, one litre of cooling water absorbs as much heat as 4 m³ of cooling air. If, for example, a calculated heat loss of 1 kW is to be dissipated, according to a common rule of thumb, a good 60 litres of water must be pumped through the cooling system per hour – or 250 m³ of cooling air. Additionally, there is no need to fear short circuits: Pure water is not conductive. It only becomes conductive through the substances dissolved in it: their ions take over the transport of electricity. Accordingly, the conductivity of seawater is 1,000,000 times (one million) higher than that of deionised water (fully demineralised).
Further information under:
https://www.schmidbauer.net/en/products/transformers/water-cooled-transformers/
Founded in 1949 in Hebertsfelden, Lower Bavaria, about 80 km east of Munich, the family-run Schmidbauer Group of Companies today is a leading global specialist in inductive components. At two locations, around 230 employees develop and manufacture all kinds of winding components, from small RF coils to large filter chokes, from regenerative mains filters to customised power supplies – including for the world’s largest particle accelerator at CERN.
A top-class development department is constantly exploring the limits of inductive components and makes the company a sought-after partner worldwide for the development of energy-efficient drives for electromobility, but also generally for power electronics used in machine tools – or in test centres for battery production. Several years ago, water cooling, for example, was considered to be some form of a "nutcase". Today, it has not only arrived in general power electronics applications, but has become a standard.
Numerous research projects and awards underline the innovative character of the family-owned company. Since 2010, the company has been continuously investing in sustainability and working to further reduce the ecological footprint of its products.
Schmidbauer Transformatoren u. Gerätebau GmbH
Spanberg 16
84332 Hebertsfelden
Telefon: +49 (8721) 9662-0
Telefax: +49 (8721) 9662-50
http://www.schmidbauer.net
Marketing
E-Mail: vr@robologs.com