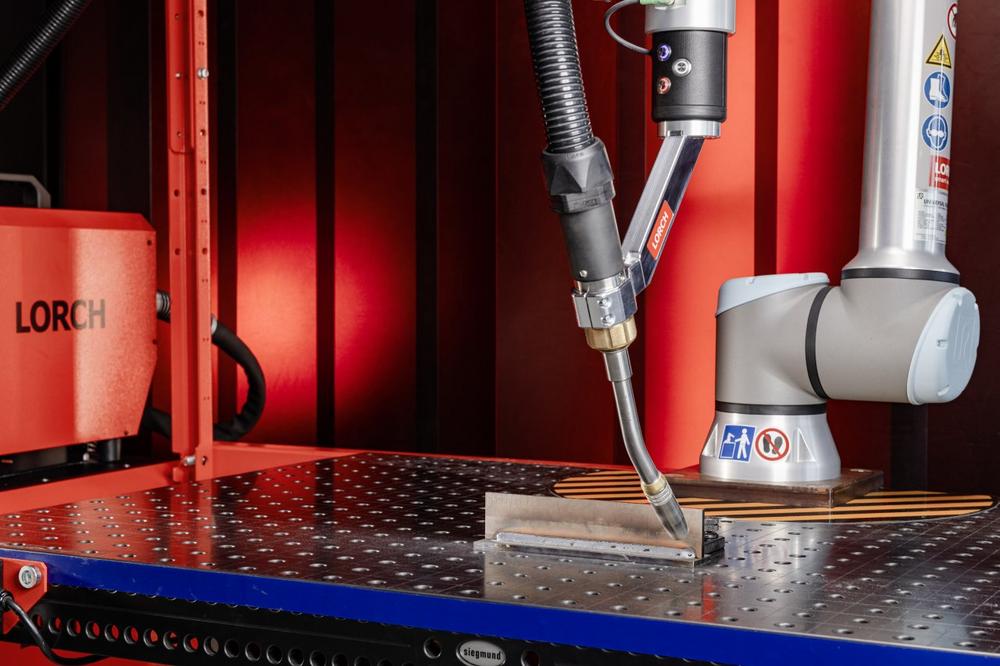
Lorch perfects Cobot welding
Since tolerance deviations and heat distortion of parts make automated welding difficult, Lorch Schweißtechnik, market leader in the field of Cobot welding, has expanded the function of its Cobot solution with the three easily programmable TouchSense, SeamTracking, and SeamPilot tools for automated seam tracking.
Automatic weld seam search with TouchSense
The new TouchSense feature allows the torch to find the weld seam position for fillet welds automatically, ensuring perfect weld seams from the very beginning. It uses the Cobot’s already-existing highly sensitive force-torque sensors for collision detection for this. The ideal torch position above the weld seam can be identified by gently touching the part with the gas nozzle. The welding wire is retracted automatically in this process to prevent any bending. When the weld seam is subsequently traced, the torch will remain well in the weld seam centre, making it possible to flexibly define torch-to-weld-seam orientation using the URCap. The best thing about it is that the Cobot will recognise and compensate for any parts placed differently another time around or any variances that may occur in the workpieces.
Ideal interaction with SeamTracking weld correction
TouchSense now allows automated welding of workpieces that used to be unsuitable for this due to their deviations. Operation also is very simple, with the welder only defining three search points on the control panel’s touch display. TouchSense is complemented by another tool: the SeamTracking assistant. SeamTracking weld correction automatically keeps the Cobot on the course of the weld seam. Lorch sensor technology will detect the arc course during the weaving movement of the torch. The smart TouchSense and SeamTracking combination in Cobot welding also easily compensates for workpiece variations. The applications can be activated in the Lorch Cobotronic software (version 4.3).
Programming complex workpieces in a matter of seconds and welding them in top quality with SeamPilot
The future of automated welding is in the SeamPilot top innovation, developed by Lorch Schweißtechnik with Fraunhofer Institute for Manufacturing Engineering and Automation IPA. SeamPilot, which helps the Cobot achieve best welding results with maximum ease of programming, is based on a line laser on the torch bracket. The operator will simply define a rough starting point. The line laser will then find and discover the weld seam to be completed and follow it to the automatically detected end point. Of course, the Cobot will keep the torch perfectly aligned with the weld seam as defined beforehand. The robot will calculate its welding path on its own, with the laser line sensor predicting the further course of the weld seam for the Cobot, permitting automatic welding even of difficult courses in curves, waves, or circles.
The technology makes welding automation enormously flexible. The smart weld seam search also enables welding of parts subject to variances, such as differently tacked workpieces. Online acquisition of the weld seam course will make it possible to weld more complex contours along the weld seam entirely without any intermediate points. SeamPilot uses one and the same program for welding component families in variant production: Automatic weld seam end detection makes it possible to weld workpieces with, for example, different length dimensions, in consistent top quality.
SeamPilot’s advantages for the user company are reflected in the enormous time savings in programming, higher flexibility, and improved Cobot utilisation at simple operation. Programming times are minimised to mere seconds without compromising welding quality. The Cobot can now automatically weld parts with variances or more complex contours, which would previously have required an uneconomically high programming effort. Finally, the number of programs will be reduced, for example, by reuse in component families.
Dr. Ing. Caren Dripke, department head of robotics development at Lorch Schweißtechnik: “TouchSense and SeamTracking make finding and tracking of seams with a Cobot easier than ever. No more than three steps need to be programmed. Feedback from our initial users has been accordingly positive: TouchSense and SeamTracking are working very well. They can be operated by anyone, and the welding quality is impeccable. SeamPilot is ringing in a new era of Cobot programming. A rough starting point is all that needs to be specified. The rest of the course will be welded automatically by seam tracking – even on complex parts, no matter where the weld seam is located and where it is leading. The welder simply determines the desired result – SeamPilot will do the rest and return best welding results.”
Lorch Schweißtechnik GmbH is a leading manufacturer of arc welding systems for industrial applications, the demanding metal craft, as well as for use in the automation with robots and collaborative robot systems. In-house developed helmet and torch systems add to ensuring optimal welding results. Lorch high-quality systems have been produced in one of the world’s most state-of-the-art welding system productions in Germany and exported into more than 60 countries for more than 65 years. Welding technology by Lorch combines great practical benefits, very simple operation, and high economic efficiency, setting new technology standards on the market.
Lorch Schweisstechnik GmbH
Im Anwänder 24-26
71549 Auenwald-Mittelbrüden
Telefon: +49 (7191) 503-0
Telefax: +49 (7191) 503-199
http://www.lorch.eu
Telefon: +49 (7191) 503-0
E-Mail: presse@lorch.eu