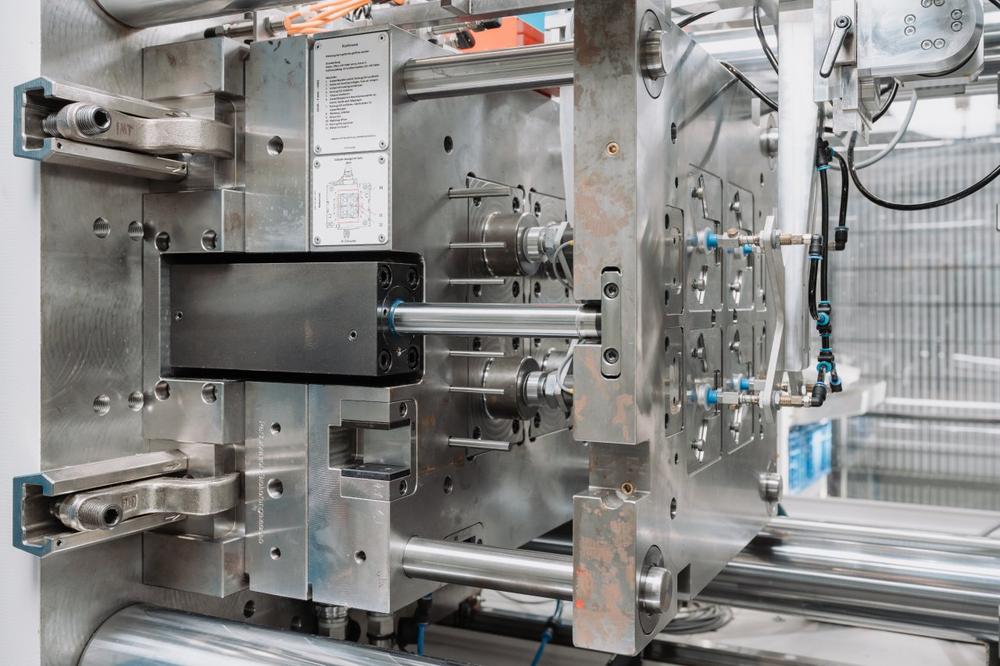
Medical technology – Innovative manufacturing chain for medical technology products
Development of the combination process
As a project partner, the Institute for Plastics Processing (IKV) in Industry and Craft at RWTH Aachen University carried out extensive process development for the combined thermoforming/backmoulding process, from a simple moulding tool to an automated 4-cavity mould (Figure 1). For this, the thermoformability of the laser-microstructured thin metal sheets in the injection moulding tool first had to be ensured, and possibilities had to be found for the handling and fixing of the thin sheet in the mould. Then the combined thermoforming/backmoulding process was analysed on a single-cavity prototype mould, and the influence of the used moulding compounds and the injection moulding parameters on the composite properties was investigated.
In cooperation with the Fraunhofer Institute for Laser Technology (ITL) in Aachen, IKV simultaneously developed suitable laser structuring parameters for the laser microstructuring, for the laser cutting process and a laser marking process. For a specific application, it is always necessary, when adjusting and arranging the microstructure geometry, to make a suitable compromise between the attainable bond strength of the plastic and metal component and the damage to the thin sheet component brought about by the structuring. The laser process was then implemented in an automatic production line. The knowledge gained was then successfully applied to a multi-cavity mould and the process was automated (Figure 2). The mould concept was selected in such a way that the number of cavities can be further increased.
Necessary requirements can be met
By systematically analysing the injection moulding process and adjusting the laser structure geometry and arrangement, it was possible, through the microform fitted plastic/metal composite to achieve strength levels that are significantly above the composite strength of 35 N required for the application. By means of laser radiation, it was also possible to create a predetermined breaking point in the sheet metal component so that the crimp caps can be reliably opened in accordance with the application.
The injection moulding parameters used have a significant influence on the attainable bond strength. In addition, a strong correlation can be observed between the bond strength and the achieved microstructure filling. The moulding compound used, the arrangement of the laser structure and the prevailing load case determine the forces required to open the crimp cap. As a supplement to the practical process investigations, the thermoforming and injection moulding processes and the microstructure filling were also simulated in collaboration with the project partner. In final tests, the flange caps were successfully steam-sterilized and crimped, thus proving their suitability for the closures of pharmaceutical vials.
By optimising the handling and the combination process, it was possible to achieve a cycle time of 45 seconds for the overall process and thus produce over 300 caps per hour. The economic efficiency of the process can be further increased in the future by raising the production speed and process reliability and also by increasing the number of cavities.
Medical technology at the 32nd International Colloquium Plastics Technology
The topics of medical technology / hybrid technology will be addressed at the Colloquium in Session 7 (Product specific process technology for injection moulding) with a keynote address and two scientific presentations from IKV.
In addition, the research assistants will demonstrate the combined manufacturing process live in the new injection moulding laboratory as part of the IKV 360° research event.
IKV, the Institute of Plastics Processing at RWTH Aachen University, is Europe-wide the leading research and education institute engaged in the field of plastics processing enjoying outstanding reputation. More than 300 staff are employed in finding solutions to problems connected with processing, materials technology and part design in the plastics and rubber industries. IKV’s close contacts with industry and science, together with its outstanding facilities, enable cutting-edge research in plastics technology and ensure that students benefit from a comprehensive, practically oriented course of study. Plastics engineering graduates from IKV are thus sought-after experts in industry. In organisational terms, IKV is divided up into the four specialist departments of Injection Moulding, Extrusion and Rubber Technology, Part Design and Materials Technology, and Composites and Polyurethane Technology. The institute also takes in the Centre for Analysis and Testing of Plastics, and the Training and Further Education department. IKV is run by an Association of Sponsors, which currently has a membership of about 300 plastics companies from all over the world. Univ.-Prof. Dr.-Ing. Christian Hopmann is Head of the Institute and Managing Director of the Association of Sponsors. He also holds the Chair of Plastics Processing at the Faculty of Mechanical Engineering at RWTH Aachen University.
Institut für Kunststoffverarbeitung (IKV) in Industrie und Handwerk an der RWTH Aachen
Seffenter Weg 201
52074 Aachen
Telefon: +49 (241) 80-93806
Telefax: +49 (241) 80-92262
http://www.ikv-aachen.de
Leiterin Presse- und Öffentlichkeitsarbeit
Telefon: +49 241 80-93672
E-Mail: rebecca.hierlwimmer@ikv.rwth-aachen.de
contact regarding medical technology
Telefon: +49 241 80-93832
E-Mail: moritz.mascher@ikv.rwth-aachen.de

