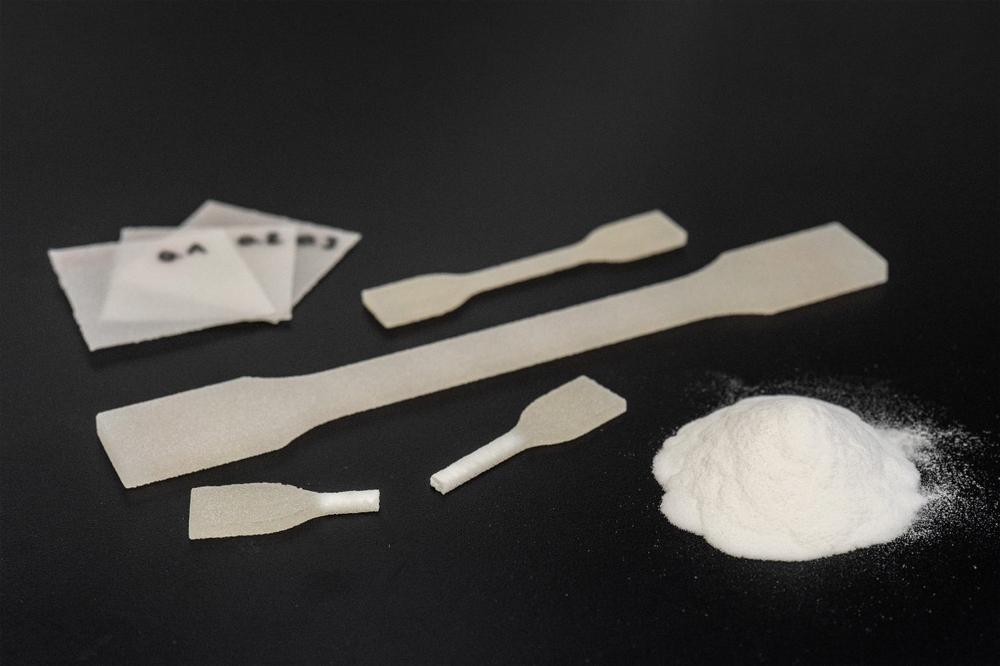
Dimensionless parameters for laser sintering
Under the direction of Dr. Johannes Rudloff and in collaboration with Dr. Claas Bierwisch from the Fraunhofer Institute for Mechanics of Materials IWM, the monolayer approach developed in the first project phase was successfully refined and validated. The results showed a high degree of agreement between numerical simulations, monolayer printing tests, energy modeling, and the results from multi-layer build jobs with polyamide 12 (PA12) and polypropylene (PP).
Faster to the optimal process window
Laser sintering (PBF-LB/P) is one of the most important processes in the additive manufacturing of plastics. However, the limited variety of materials remains a key challenge. To address this, the project team combined numerical simulations with material and process data to analyze the energy conversion in the process using dimensionless parameters for PA12 and PP powders.
A suitable process window was identified through simple monolayer printing tests with different energy inputs and subsequent thickness measurements.
This resource-saving approach enables significant time savings in process development. The optimum point of the applied surface energy density is defined by the intersection of the two dimensionless parameters for energy input and energy requirement – i.e., where their difference is zero.
Validation through mechanical tests
To verify the predicted parameters, tensile test specimens were manufactured and mechanically tested. The results confirmed the practical suitability of the approach:
With similar values for energy input and demand, the best mechanical properties were achieved for PA12 and PP. This underlines the potential of the monolayer approach as an effective tool for the fast and reliable identification of suitable process parameters – even for novel materials.
Multilayer tests and influence of interlayer time
In addition, multilayer tests were carried out to investigate the influence of interlayer time (ILT) on component properties. The results showed an increase in density at higher ILTs – in line with the simulations.
Conclusion
The project makes a significant contribution to the further development of laser sintering and the integration of new materials into additive manufacturing. The methods developed enable faster, more efficient, and scientifically sound process development—an important impetus for research and industry. Further funded implementation projects are in preparation and are scheduled to start within the next six months.
This completes the project "Numerical and experimental investigations of dimensionless material parameters in the generative manufacturing of polymers by laser sintering – Part 2: Expansion of the field of application" (funding code BA 1841/32-2), which started on January 1, 2022, and ran until June 30, 2025, has been successfully completed.
Including the first sub-project, this marks the end of almost seven years of funding. The aim of the project was to better describe the powder bed fusion (PBF) process using dimensionless parameters, thereby significantly accelerating the parameter determination for new materials and process optimization.
The SKZ welcomes inquiries from industry regarding the application of simulations and dimensionless parameters for targeted material development and process design.
The SKZ is a climate protection company and a member of the Zuse Association. This is an association of independent, industry-related research institutions that pursue the goal of improving the performance and competitiveness of industry, especially SMEs, through innovation and networking.
FSKZ e. V.
Friedrich-Bergius-Ring 22
97076 Würzburg
Telefon: +49 931 4104-0
https://www.skz.de
Business Unit Manager | Material Development | Compounding | Extrusion
Telefon: +49 (931) 4104-528
E-Mail: j.rudloff@skz.de

