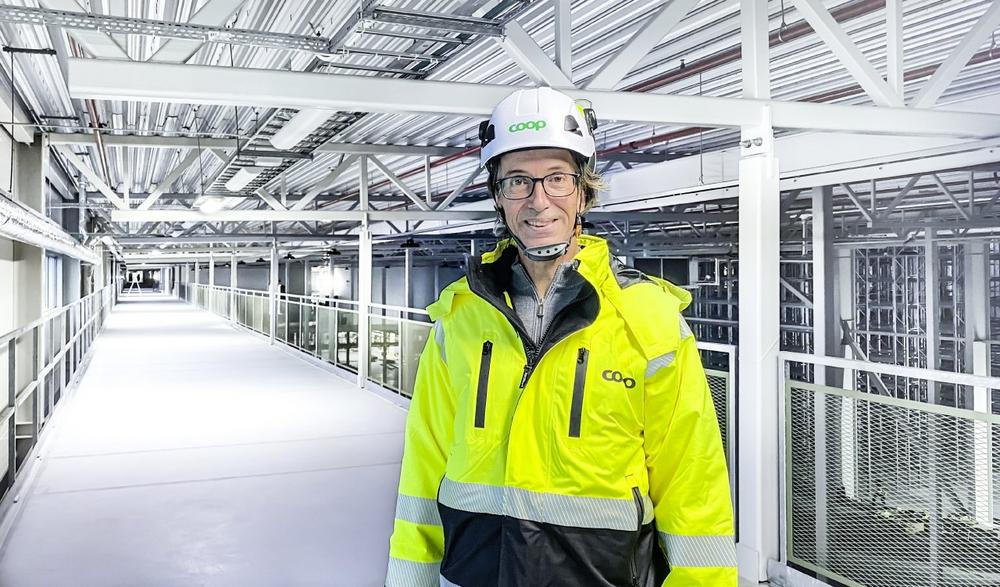
From manual to one of the largest automated distribution centers
“We have seen many shifts to automation within our industry. The productivity rates reached with the automated operations are impossible to get with the manual goods handling,” shares Mats Tornard, Project Manager of Strategic Supply Chain at Coop.
Thinking about the working environment for the employees, long-term future and continuous efficiency, Coop made the strategic decision to invest in a new highly automated logistics center.
Everything in stock: How the system installed on 77,000 sq.m. will work
Coop’s values were clearly communicated at the beginning of the project so that no compromises had to be made. Keeping the main focus on employees and sustainability the retailer considered them in every decision it had to make regarding the new facility. For starters, goods delivery will be linked with the nationwide train network to reduce car use and, as a result, the CO2 footprint.
Most of the inbound goods will arrive at the new distribution center by train and will be unloaded just outside of the infeed area. The goods receiving zone will be equipped with a conveying system including a NOK station and also a pallet check station to see whether wrapping, positioning and load handling were done correctly. Then the goods will be delivered to the high bay warehouse for storage until they are requested for an order. The pallets then will arrive at the depalletizing station to be divided into individual cases for storing and preparing for later-on commissioning to customer orders.
The 3D-Matrix Solution® by SSI Schaefer, which the client calls “picking storage”, is intended to serve as a buffer for cases. The storage locations will be operated by SSI Flexi shuttles, which are responsible for storage loading and retrieval. The needed sequence for palletizing will be automatically pre-determined and controlled via SSI Schaefer’s own logistics software WAMAS® depending on the contents of orders, guaranteeing both pallet stability and minimal transport volume. SSI Flexi will then deliver cases to the palletizing station where a palletizing robot will take care of putting the orders together for shipping.
Ready pallets will be delivered to the shipping buffer where all the loads coming to one customer or location will be consolidated awaiting departure. Finally, the trucks will arrive and pallets will be retrieved in loading sequence to the shipping doors.
“Sometimes it is complicated to make things easy, but I believe we managed to create an amazing solution together,” says Mats Tornard.
Where we are now
“Despite all the challenges the pandemic brought to the market, we are happy that we are on schedule with the project realization and have not experienced any delays so far,” comments Mats Tornard. “We have just completed construction of the distribution center. SSI Schaefer is now building up the high bay warehouse and the SSI Flexi shuttle racks. At the same time, we are also focused on redesigning our internal processes to benefit the most from the new system.”
Benefits and no doubts
“It is great that both companies see this cooperation as a long-term partnership. We are happy to see that SSI Schaefer is always committed to bringing forward their new solutions that were not available earlier at the layouting and designing stages. This proactive and innovative thinking will definitely help us to realize the maximum potential of our distribution center,” says Mats Tornard.
The new facility will help Coop to boost its supply chain performance. Coop will get a great increase in the number of daily shipped orders and more accessible and perfectly scheduled transportation owned to the better railroad connection.
Coop aims at reducing unloading time at the stores by providing customer friendly pallets, delegating palletizing to palletizing robots as part of the SSI Case Picking system. It will add up to the current effort and ensure faster and more solid build-up of the pallets.
One of the key advantages the solution is expected to deliver is a safer and more ergonomic work environment. At the currently operating site, all the processes are done manually, which includes lifting and carrying heavy weights, stretching etc. When the new solution is launched, most of the challenging jobs will be performed by automated equipment that mainly requires monitoring and controlling functions from people. This will enable Coop and its employees to shift the focus from potential health-related concerns to the strategic thinking of what else can be done to improve the outcome.
Sustainable future around the corner
“Sustainability is one of Coop’s core values,” explains Mats Tornard.
And it has been this way for years. For example, 30 years ago the company was the first food chain in Sweden to launch its organic brand, Änglamark. The brand is well-known across Sweden and preserves its initial value – an eco-friendly approach. Thus, in 2020 Änglamark was named Sweden’s most sustainable brand by Sustainable Brand Index. This year the award again went to Coop.
Mats Tornard continues: “We always consider environmental and ecological aspects before starting a new project.”
The new solution will also bring more sustainable benefits to the company. By moving cold and ambient storage zones into one facility, Coop will require less transportation and, therefore, will create a less CO2 footprint.
Coop is already using trains to receive goods because it is more environmentally friendly. For the new distribution center, the train capacity will be twice more than today. Two sets of railroads will run right next to the warehouse to ensure smooth and fast unloading. The trains will be enlarged to the maximum approved length. With this solution, Coop will be able to support the upcoming growing demand without the need of utilizing other vehicles, e.g. trucks.
“Coop is a company of great individuality, sustainable approach and deep care for its employees. SSI Schaefer shares the same values. This is one of the reasons behind the prosperous and seamless cooperation between our companies. We are delighted to be a part of such an exciting project,” – concluded Michael Hillström, General Manager of SSI Schaefer in Sweden.
The SSI Schaefer Group is the world’s leading provider of modular warehousing and logistics solutions. With headquarters located in Neunkirchen (Germany), SSI Schaefer employs approximately 10,000 associates globally, along with seven domestic and international production sites, and approximately 70 worldwide operating subsidiaries. Across six continents, SSI Schaefer develops and implements innovative industry-specific answers to its customers‘ unique challenges. As a result, it plays a key role in shaping the future of materials handling.
SSI Schaefer designs, develops and manufactures systems for warehouses and industrial plants. Its portfolio includes manual and automated solutions for warehousing, conveying, picking and sorting, plus technologies for waste management and recycling. In addition, SSI Schaefer is now a leading provider of modular, regularly updated software for in-house material flows. Its software team, with a headcount in excess of 1,100, develops high-performance applications, and provides customers with in-depth advice on the intelligent combination of software with intralogistics equipment. The SSI Schaefer IT offering, including its own WAMAS® and SAP products, delivers seamless support for all warehouse and material flow management processes. Solutions from SSI Schaefer improve the productivity and efficiency of customer organizations – not least through the highly precise monitoring, visualization, and analysis of operational metrics for proactive intralogistics management.
SSI Schaefer offers highly sophisticated, turnkey systems. As an international player, it can deliver one-stop solutions to all four corners of the earth. Its comprehensive portfolio encompasses design, planning, consulting, and customer-specific aftersales services and maintenance.
SSI SCHÄFER
Fritz-Schäfer-Strasse 20
57290 Neunkirchen / Siegerland
Telefon: +49 (2735) 70-1
Telefax: +49 (2735) 70-396
http://www.ssi-schaefer.de
Marketing & Kommunikation
Telefon: +49 (2735) 70-252
Fax: +49 (2735) 70-382
E-Mail: melanie.kaempf@ssi-schaefer.de
Junior Project Manager CR & PR | Global Marketing
Telefon: +49 (2735) 70-9683
Fax: +49 (2735) 70-382
E-Mail: Annika.Nolte@ssi-schaefer.com

