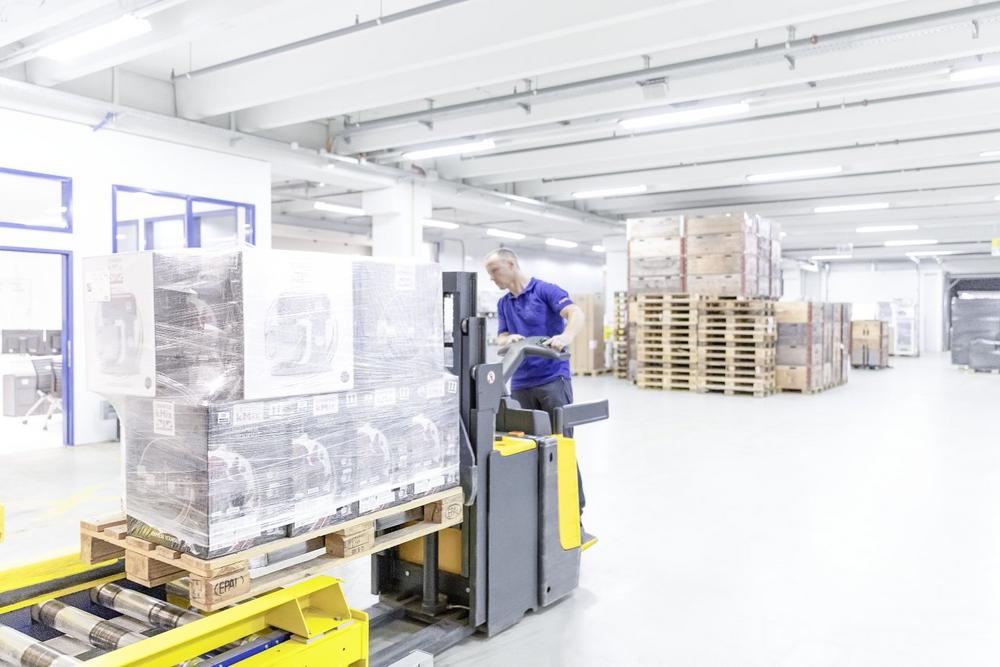
From Retail Logistics to High-Performance Multi-Channel Logistics
With over 2,000 employees, 150 branches nationwide and revenue of more than CHF 1 billion, the Fust company is now one of Switzerland’s ten largest retailers. Since the end of 2007, Dipl.-Ing. Fust AG has also been an independent subsidiary of the Coop group. The Fust Group includes RS Vertriebs AG, integrated in 2020, with its nettoshop.ch division, as the market-leading online retailer for home electronics in Switzerland.
Flexible Intralogistics for E-Commerce
In view of the dynamic development of e-commerce, attempts are often made to handle order volume increases by increasing staffing levels and leasing external warehouses. However, even before the pandemic began, Fust decided against such an ad hoc solution. As early as 2016, this Coop subsidiary was looking to increase the level of automation of its intralogistics processes. This re-orientation was intended to reflect the strong ongoing growth of the company, which was originally anchored solely in the retail sector. The core objective was to expand and centralize warehouse capacity at the Oberbüren site. Moreover, to optimize cycle time, reduce handling time in small parts picking and, of course, reduce the logistics costs. One of the biggest challenges was to find an intelligent project solution on the process and technology level that would meet the specific needs of supplying branches and online retailing equally efficiently.
A Scalable Mix of Solutions from a Single Source
The warehouse has been in operation since 2003. To modernize the warehouse, as well as turning it into a highly efficient multi-channel logistics center, another objective of was to simplify the complex process of managing the various suppliers, which required significant time and effort for coordination. Thanks to SSI Schaefer’s broad product portfolio, all these needs could be met with solutions from a single source: bin storage with the SSI Cuby one-level shuttle system, high-bay warehouses, solutions for manual areas and its high-performance WAMAS software. The fact to get everything from a single source engendered confidence and trust, allowing to maintain a collaborative partnership right from the start. The project began with a signed contract in June 2017. Once the construction work was completed, installation began in October 2018; by August 2019, the partners were ready to announce the successful go-live of the entire new system.
40% Picking Performance Increase
Maximum Availability through Innovative Technology
Throughout the course of the project, the importance of a high degree of flexibility on both the module and the software level became apparent. In the original planning, the ratio of branch supply to e-commerce was 70 to 30, but this flipped completely with the onset of the pandemic – peak days saw a ratio of 10 to 90. This corresponds to a rapid increase in packages, to as many as 7,800 packages per day in some cases. “The system itself stood up to this onslaught and achieved availability of 99 percent with the usual high reliability,” reports Tim Langenbach, Director of Business Development for Retail & Wholesale/Food Retail at SSI Schaefer. “What makes the difference is the perfect interplay between SSI Cuby, the technological heart, on the one hand and the WAMAS logistics software, the brain of the system, on the other.” In addition to the intelligent control, the software’s intuitive operation has also allowed a quick response. Both employees and branch workers could be trained quickly, making an important contribution to significantly increasing picking performance. SSI Schaefer upgraded the server capacity in parallel within a very short time frame. The WAMAS solution, which was designed for high transaction volumes, was able to ensure smooth operation.
An Ergonomic Process Design that Saves Space
After picking, an intelligent gantry robot stacks the containers for delivery to branches completely automatically, which significantly reduces the employees’ workload and ensures continuous material flow. Both the gantry robot and the grippers were developed and integrated by the Schaefer Group company, RO-BER. The customer packages are then packed and shipped through twelve ergonomic workstations.
As in the ASPW, optimum space utilization was also achieved in the automated high-bay warehouse (HBW). The rack system is designed to function as the roof support, allowing double-deep storage of more than 15,000 pallets. The three aisles are served by energy-efficient SSI Exyz-type storage retrieval machines. Items can be stored in and retrieved from all five levels of the HBW. Picking from the HBW is also supported by two goods-to-person workstations and a retrieval device for full pallets.
Digital Transformation of Multi-Channel Logistics
With its in-house WAMAS logistics software, SSI Schaefer has already implemented a uniform Warehouse Management System (WMS) at numerous Coop Group warehouse locations since 2001. Fust now also benefits from the performance and quality improvements that have been achieved by connecting the central WMS. The result is complete transparency and traceability of all transactions and information flows. In addition to the WAMAS WMS, Fust also uses the WAMAS Warehouse Control System (WCS). The WCS controls the relevant processes in the warehouse in real time and organizes, sequences and synchronizes all automated warehouse resources. If conditions change, the system reprioritizes. This has achieved significant advantages in terms of data depth, transparency and process reliability.
Ready for the Future Thanks to Maximum Flexibility
Thanks to the new intralogistics mix, Fust now has the tools it needs to further assert itself on the market successfully and handle future growth. It also retains flexibility given the backdrop of volatile market changes. The hardware and software are scalable, providing the foundation Fust needs to meet the future demands of online business. The logistics concept, as it was originally agreed, was primarily geared towards the retail trade; through a collaborative partnership, the company has successfully adapted it to the e-commerce boom. While the original assumptions foresaw a productivity increase of 20%, this was far exceeded by the actual increase of 40%. “SSI Schaefer’s intelligent multi-channel solution puts us in a flexible position to support ongoing growth in the future,” summarises Daniel Marbach.
The SSI Schaefer Group is the world’s leading provider of modular warehousing and logistics solutions. With headquarters located in Neunkirchen (Germany), SSI Schaefer employs approximately 10,000 associates globally, along with seven domestic and international production sites, and approximately 70 worldwide operating subsidiaries. Across six continents, SSI Schaefer develops and implements innovative industry-specific answers to its customers’ unique challenges. As a result, it plays a key role in shaping the future of materials handling.
SSI Schaefer designs, develops and manufactures systems for warehouses and industrial plants. Its portfolio includes manual and automated solutions for warehousing, conveying, picking and sorting, plus technologies for waste management and recycling. In addition, SSI Schaefer is now a leading provider of modular, regularly updated software for in-house material flows. Its software team, with a headcount in excess of 1,100, develops high-performance applications, and provides customers with in-depth advice on the intelligent combination of software with intralogistics equipment. The SSI Schaefer IT offering, including its own WAMAS and SAP products, delivers seamless support for all warehouse and material flow management processes. Solutions from SSI Schaefer improve the productivity and efficiency of customer organizations – not least through the highly precise monitoring, visualization, and analysis of operational metrics for proactive intralogistics management.
SSI Schaefer offers highly sophisticated, turnkey systems. As an international player, it can deliver one-stop solutions to all four corners of the earth. Its comprehensive portfolio encompasses design, planning, consulting, and customer-specific aftersales services and maintenance.
SSI SCHÄFER
Fritz-Schäfer-Strasse 20
57290 Neunkirchen / Siegerland
Telefon: +49 (2735) 70-1
Telefax: +49 (2735) 70-396
http://www.ssi-schaefer.de
Junior Project Manager CR & PR | Global Marketing
Telefon: +49 (2735) 70-9683
Fax: +49 (2735) 70-382
E-Mail: Annika.Nolte@ssi-schaefer.com
Marketing & Kommunikation
Telefon: +49 (2735) 70-252
Fax: +49 (2735) 70-382
E-Mail: melanie.kaempf@ssi-schaefer.de
