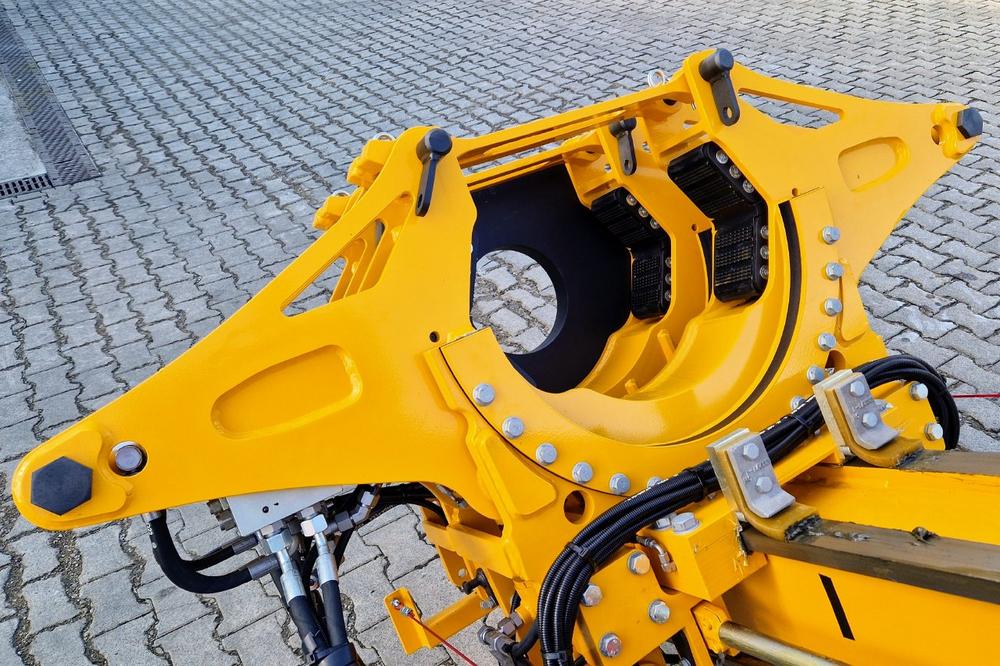
KLEMM drilling rigs – Innovations and a look to the future
The task of improving a standardized machine part, such as a clamping and breaking unit, has been one such internal project carried out over the last one and a half years.
The clamping and breaking unit which is one of the most highly stressed machine elements on the drill rig fulfills numerous tasks within the drilling operation. These varying tasks call for an understanding of each individual function and how they can affect each other. The goal being to optimize the working procedure and the lifespan of these rugged machine elements.
Repositioned Cylinders
The clamping cylinders (position 1) found on both the clamping and the breaking units have been rotated by 180° to reposition the piston rods and the wiping seals out of the direct line of the drill cuttings. “This reduces the possibility of drill cuttings damaging the wiper seals and subsequently entering and contaminating the hydraulic system.” explained Martin Bonzel.
An additional benefit is, that when drilling to greater depths, the transfer of weight force from the drill string to the clamping jaws is no longer carried solely by the piston rods. The much larger cylinder outer body, which has been designed with rails to fit exactly into the unit housing, allows for the forces to be carried not only by the cylinder body itself but also by the complete clamping and breaking housing. This simple, but effective design change will substantially reduce the number of damaged cylinder rods and seals.
Improved Clamping Jaws
Fixed clamping jaws (position 2) are designed to hold a specific diameter when the contractor predominantly uses the same size of tooling on each jobsite.
The latest development is a movable clamping jaw (see positions 3) which adjusts itself according to the actual diameter of the tooling being used. This is the ideal clamping tool when a large range of different diameters are commonly used.
Jaw inserts made from carbonated high alloyed steel
New style of jaw inserts (position 4) made from carbonated high alloyed steel which will increase the life cycle of the inserts and offer more grip on the drill tool. This additional grip allows for a reduced clamping pressure, which will subsequently decrease any deformation to the threaded adapters of the drill tools.
High Wear Plastic Rails
Integrating replaceable high wear plastic rails (position 5) on surfaces with relative movement will reduce the need for subsequent costly maintenance work as the metal machine parts no longer come into contact with one another.
Open face clamping
The opening area of the clamp (position 6). In the past, the necessity for longer clamping jaws to hold augers across the pitch of its flights has reduced the maximum possible diameter of the augers. This problem has been addressed by opening up the area around the jaws i.e. a 14” clamp could previously accommodate an auger diameter of only 8 1/2”. The new opening of the passage area on the housing has enabled this diameter to be extended to 13”.
Stand Alone Unit
“Whilst taking a new look at the clamping and breaking units, we decided to design them as standalone devices” said Martin Bonzel, “This meant integrating all the necessary hydraulic valves into the unit itself and ensuring that the central height of the drill string axis to the central axis height of the rotary heads and drifters remains the same. This allows for an easy swap of complete units”.
In practice this means that when moving, for example, from a tie-back to a micro-pile jobsite, with the need to change the clamping and breaking unit from a 10” diameter to a 14”, or even 17” diameter, the units can be considered as interchangeable. This idea has not only been implemented on a particular machine model, but where possible, across the whole range of different machine models – therefore making it a truly modular system.
The clamping and breaking unit described is presently on field test in Europe and will be released as a standard product in the near future. A scaling in size to additional larger and smaller diameters is presently being undertaken.
These examples show that seemingly standardized machine elements have great potential for improvement, and when adapting them to the ever-changing requirements of modern jobsites and drilling operations much can be achieved.
Outlook into New Technologies. Zero-Emissions.
Another area of great focus is the electrification of the drilling rigs. “We are seeing more and more inquiries for electrically powered machines with the aim of reducing the carbon footprint on the construction jobsite.” Carl Hagemeyer said. Drilling rigs with electric asynchronous motors that are connected directly to the mains have been part of the construction industry for many years. The engineering challenge now is to explore the different avenues of how best to power the machines of the future.
KLEMM’s first venture into such technologies was shown in October 2022 at the Bauma exhibition in Munich.
“On our journey to Zero-Emissions we have developed a hybrid power train with a 125 A (86 kW) plug-in connection which works in conjunction with a battery backpack (140 kWh). As we know that the average energy consumption of an anchor drilling rig is about 25-35% of the installed power and considering the power consumption of the diesel-hydraulic drilling rig with 175 kW we were able to develop this hybrid system accordingly.” Carl Hagemeyer, said. The batteries act as a buffer to supply peak power needs when the 86 kW from the grid is exceeded. Once the power demand drops below the 86 kW threshold (e.g. when idling or rod changing) the excess power is used to recharge the battery. This is achieved with the help of our inhouse developed energy management software, allowing the machine to re-charge whilst operating without any downtime.
An additional benefit of the hybrid system is the “off grid operation” capability, which can be necessary in situations where the operation of the drilling rig is required without the availability of the electrical grid. Examples for such situations would be when loading or unloading the drilling rig on inner city streets or at remote locations where the machines’ access point to the construction site and the actual drilling area are some distance apart. A simple off-grid driving of the machine is then possible.
A power concept for special high-power applications is a 2 x 125 A plug system without battery backpack, which provides 2 x 86 kW (= 172 kW). So, maximum power is provided constantly. This system can be utilized effectively on jobsites when connected directly to the mains. For loading and unloading purposes the machine can be powered by an easy to come by 32 A or larger power outlet.
The first deployment of a KLEMM KR 806-3E hybrid machine is due in late spring or early summer of 2023 on a large micro-pile jobsite in the Netherlands. “Our engineers will of course be monitoring the progress and applying this field knowledge accordingly”, Carl Hagemeyer said.
Although there still lies some engineering and innovation ahead to make this Zero-Emission rig a standard drilling rig on construction sites all over the world, the progress made here is very tangible.
KLEMM Bohrtechnik looks forward to reporting on further developments in these new and exciting fields as time progresses and will finish by saying, for standard machine elements or new drive concepts, innovation never stops…..
KLEMM Bohrtechnik is a world-leading specialist for the development of exceptionally high-quality and powerful drilling rigs with total weights of up to 32 tonnes. The special feature: world-leading technologies which make KLEMM drills unrelenting.
As a market pioneer, KLEMM has had a decisive influence on the development of anchor drilling technology over the last five decades. This has lead to a technological advantage from which customers around the world benefit. This is because KLEMM offers a broad range of products and services (drilling devices, hydraulic hammers, rotary drives and drilling equipment) as well as individual solutions so that customers can carry out drilling tasks as best as possible with regard to time required, efficiency, reliability and safety.
KLEMM Bohrtechnik GmbH
Wintersohler Str. 5
57489 Drolshagen
Telefon: +49 (2761) 705-0
https://www.klemm.de
Telefon: +492761705138
E-Mail: martin.bonzel@klemm.de

