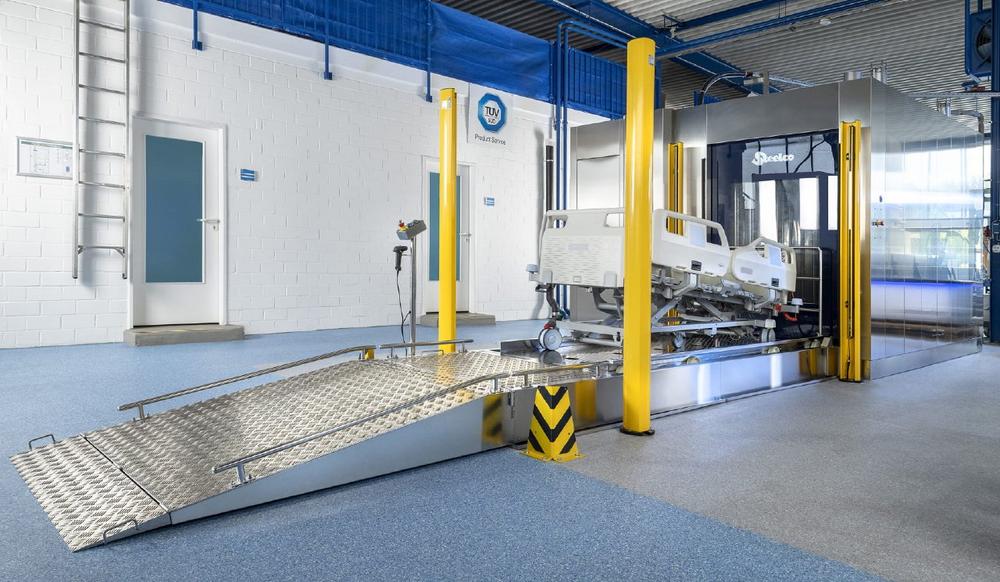
TÜV SÜD tests machine-washability of medical devices
The automated washing system now enables TÜV SÜD’s experts to conduct tests verifying how aspects such as surface finishes, integrated electronics, plastic paneling and movable parts like bearings and brakes withstand the washing process. “All cavities must be watertight, and drive system housings must be installed in such a way that they are protected against temporary immersion”, explains Torsten Zimmer, Department Head of Medical & Health Services Testing Hanover at TÜV SÜD. “Our Hanover washing system simulates washing cycles for different medical devices.” While manufacturers previously had to invest in their own washing system or use those of hospitals, Zimmer points out that “our experienced experts can rapidly deliver the required proof”. At the same time, positive proof of testing increases product value and manufacturers can use the proof for product promotion.
Testing in compliance with standards
TÜV SÜD tests, for example, how many washing cycles certain medical devices must withstand. For medical beds, this is assessed on the basis of DIN EN 60601-2-52, which requires durability with 50 washing cycles. In the current draft standard addressing beds for medical use, the number of test cycles required has been increased to 250, while DIN EN ISO 10535 for patient hoists and ISO 19894 for walking aids each specify 50 test cycles. TÜV SÜD has developed the corresponding test procedures on this basis. First, the devices are exposed to a temperature pre-treatment for 10 days, followed by washing, rinsing and cooling. “The time factor, the water or air temperature, but also the pH value and the dosage of the added cleaning, disinfection and rinse agent are important here,” says Torsten Zimmer. “With our new washing system, we ensure that the products remain safe and functional in the intensive daily hospital routine,” the expert continues.
Example bed cleaning
In Germany, 20 million people are treated as hospital inpatients annually. The beds they occupy are cleaned before every new patient, a process involving not only changing linen and bedding, but also cleaning the mattress and the bed itself. Machine reprocessing is being used more and more frequently for this purpose. The beds are first taken to a central department for reprocessing, pushed into the machine and the cleaned, disinfected and dried at the push of a button. Although transporting the beds is a logistical effort, the cleaning result is consistently reliable. Among its benefits, it eases the workload of the nursing teams and reduces contact with potentially infectious surfaces by cleaning staff.
Reliable hygiene offers protection and reduces workloads
Decision-makers in hospitals and other care facilities often specifically seek out for medical devices that can be reprocessed by machine when purchasing. As the care industry comes under increasing pressure from competition and rising costs – a situation exacerbated by the COVID-19 pandemic – more efficient and reliable cleaning processes are necessary. Patients and nursing staff need reliable protection from infection, whether it is caused by viruses, bacteria or multi-resistant germs. According to the Robert Koch Institute, the number of hospital infections in Germany is between 400,000 and 600,000 per year1.
Sustainability aspects of the testing facility
“We will reuse about 75 per cent of the water used. This means that per wash and rinse cycle, approximately 160 litres of the 210 litres required will be recycled and reused. This saves a lot of energy and water and is thus another contribution to achieving TÜV SÜD’s sustainability goals,” adds Torsten Zimmer. Additional optimisation and savings measures are currently undergoing consideration, including heat recovery from the remaining wastewater as well as carbon-neutral energy generation through photovoltaics.
1) https://www.rki.de/DE/Content/Service/Presse/Pressemitteilungen/2019/14_2019.html
Founded in 1866 as a steam boiler inspection association, the TÜV SÜD Group has evolved into a global enterprise. Over 26,000 employees continually improve technology, systems and expertise at more than 1,000 locations in around 50 countries. They contribute significantly to making technical innovations such as Industry 4.0, autonomous driving and renewable energy safe and reliable. www.tuvsud.com
TÜV SÜD AG
Westendstraße 199
80686 München
Telefon: +49 (89) 5791-0
Telefax: +49 (89) 5791-1551
http://www.tuvsud.com/de
Pressesprecher
Telefon: +49 (89) 5791-1592
Fax: +49 (89) 5791-2269
E-Mail: Dirk.Moser-Delarami@tuvsud.com
