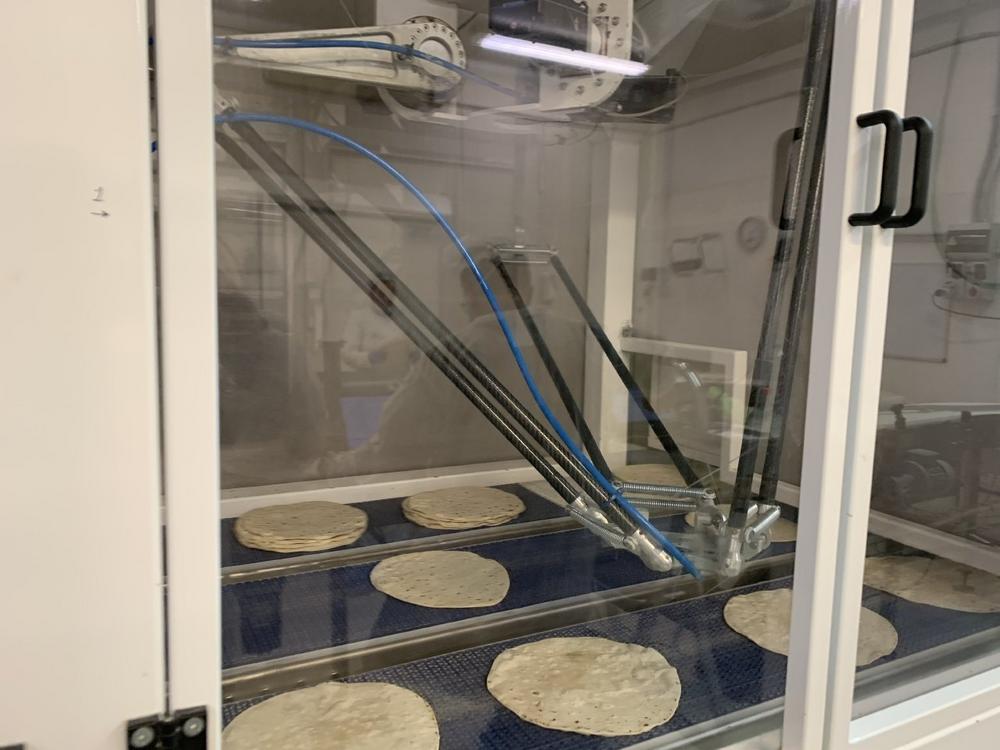
Piadine unter Kontrolle
Der italienische Dichter Giovanni Pascoli nannte sie „das Brot oder vielmehr das Nationalgericht der Menschen in der Romagna“. Ihr Ursprung geht auf die Zeiten der alten Römer zurück. Aber noch heute ist die Piadina unter Erwachsenen und Kindern sehr beliebt. Im Laufe der Jahre hat die Piadina-Herstellung die Grenzen Italiens überschritten und im Ausland schnell Verbreitung gefunden – stets mit großem Erfolg. Nach den Daten des Konsortiums zur Förderung und zum Schutz der Piadina Romagnola ist die Piadine-Produktion im Jahr 2020, auch aufgrund der Covid-19-Pandemie, rapide angestiegen und hat 22.030 Tonnen erreicht. Dies entspricht einer Steigerung von 23,3 % gegenüber dem Vorjahr. Um die wachsende Nachfrage des Marktes bedienen zu können, sind gut funktionierende Produktionslinien unerlässlich.
Pick-and-Place-System mit Optimierungsbedarf
Aus diesem Grund wandte sich ein Piadina-Produktionswerk in der Provinz Rimini an den Systemintegrator Bosso Automazioni (www.bosso.it). Das seit 2001 aktive Unternehmen aus Rimini konstruiert als Systemintegrator kundenspezifische Maschinen und stützt sich bei der Umsetzung seiner innovativen Ideen auch auf eine Partnerschaft mit Yaskawa.
Diese Zusammenarbeit hat es ermöglicht, das Pick-and-Place-System der Anlage, welches zum Stapeln der Piadine für die Verpackung verwendet wird, zu überarbeiten. Das frühere System war stark veraltet, basierte auf einem unzeitgemäßen Ansatz und enthielt Komponenten (wie z. B. Kameras), die nicht dem Industriestandard entsprechen.
Mit ihren zwei Delta-Robotern, die jeweils von einer separaten Steuerung mit MECHATROLINK-IISchnittstelle und Sigma-7-Servomotoren geführt wurden, hatte die Produktionslinie nie die gewünschten Ergebnisse erzielt. Selbst mit dem Einsatz eines zusätzlichen Roboters waren die Probleme geblieben: geringer Wirkungsgrad, mangelhafte Produktaufnahme, häufige Komponentenausfälle, Überlastung der Verstärker. Mit den höheren Produktionsraten, die zur Deckung der Spitzennachfrage erforderlich sind, hätten sie sich vermutlich noch verschlimmert.
Höchste technische Anforderungen
Die Anforderungen des Endkunden waren deshalb klar: Beseitigung der Steuerungs-, Zuverlässigkeits- und Zyklusprobleme, Erhöhung der Produktivität auf 85 Piadine pro Minute (5.100 Piadine/Std.), Reduzierung des Ausschusses auf unter 3 %, Verbesserung der Lebensdauer der verwendeten Geräte, der Motorabstimmung und der Qualität der Bewegungsabläufe, um Ausfälle der Servomotoren zu vermeiden bzw. zu verringern. Zusätzlich zu all diesen Anforderungen sollte versucht werden, den Umfang der Änderungen am bestehenden System so gering wie möglich zu halten.
Die Komplexität der Anwendung war beträchtlich: Das Aufnehmen und Ablegen der Piadine sollte zwischen gegenläufigen Förderbändern stattfinden. Der Vorgang erfordert eine extreme Variabilität, sowohl in Bezug auf die Form als auch auf die Positionierung. Für das Aufnehmen und das Ablegen ist daher der Einsatz von Conveyor-Tracking-Funktionen an den laufenden Bändern erforderlich. Die Piadine werden in unregelmäßigen Abständen aus einer langen Backlinie mit anschließender Abkühlung herausgefahren. Hinzu kam eine weitere Kundenanforderung: Die Verpackungen, die eine variablen Anzahl enthalten, sollten ästhetisch ansprechend aussehen. Als oberstes Produkt muss eine Piadina mit den typischen dunklen Röstspuren für den Verbraucher sichtbar positioniert werden.
Um die Anwendung zu steuern, wurde eine Lösung benötigt, die mit einer Vielzahl von (auch nichtindustriellen) Komponenten zusammenwirken kann. Die Maschinensteuerung MP3300iec RBT wurde auf Firmware-Ebene in die Steuerung integriert. Man entschied sich für die Verwendung einer einzigen Steuerung für die gesamte Anlage, wodurch das Konzept der „singulären Steuerung“ konkretisiert wurde und die in Wechselwirkung stehenden Funktionen der Komponenten selbst besser gesteuert werden konnten.
Simulation bei laufender Produktion
Doch damit nicht genug, ein weiterer Faktor verkomplizierte die ohnehin schon schwierige Situation: Da es sich bei dem Endanwender um einen Supermarktlieferanten handelt, der im 3-Schicht-Betrieb arbeitet, konnte die Produktionslinie während der Migration auf die Yaskawa-Komplettlösung nicht unterbrochen werden.
Die zu berechnende Dynamik war komplex, sowohl wegen der hohen Variabilität als auch wegen der Verwendung einer Kamera (anstelle eines echten Vision-Systems). Die Kamera war außerhalb des Roboter-Arbeitsbereichs positioniert, was die Kalibrierung zusätzlich erschwerte.
Zur Anwendung gehörten auch Nicht-Yaskawa-Roboter, so dass die Wahl auf die Maschinensteuerung MP3300iec RBT fiel. Da zuvor keine Praxistests möglich waren und die Produktion nicht gestoppt werden durfte, entscheid sich das Yaskawa-Team dazu, die Effizienz der Sortieralgorithmen in einer Simulation über das HMI-Panel der Zelle zu testen.
Die Idee war, die Anwendung auf dem Simulator zu entwickeln und zu testen und dann von der Simulation auf die reale Maschine zu wechseln. Die Ergebnisse waren überzeugend: Die maßgeschneiderte Simulation erlaubte es, das Lastmanagement zu optimieren und die Geschwindigkeit der Roboter schnell anzupassen. Als die reale Zelle in Betrieb war, erlaubte der Simulator die Visualisierung des Prozesses in Echtzeit. Dank der Flexibilität der für die Anwendung entwickelten Algorithmen konnte auch die charakteristische Unregelmäßigkeit der ankommenden Produkte perfekt gemanagt werden. Das Ziel, etwa 6.000 Piadine pro Stunde zu stapeln, wurde erreicht, und der Prozentsatz der Ausschussware wurde auf null reduziert.
Erfolgsfaktoren und Ergebnisse
Das Know-how von Yaskawa in den Bereichen Datenerfassung, Risikoanalyse und Projektmanagement war der Schlüssel zum Erfolg dieser Anwendung. Von großer Bedeutung war auch das Ergebnis in Bezug auf die Energieeffizienz: Während ursprünglich jeder Delta-Roboter über eine eigene Steuerung geführt wurde, gibt es nun für die gesamte Lösung eine singuläre Steuerung. Die kumulative Last wurde von auf 55 % des ursprünglichen Werts reduziert und die Servomotoren wurden von 1,0 kW auf 750 Watt verkleinert.
Zusammengefasst, ermöglichte es die Optimierung der Bewegungsabläufe, die durchschnittliche Lebensdauer der Anlage zu verlängern, die Betriebskosten zu senken, Ausfallzeiten und Ausschuss zu vermeiden und somit die Anlage insgesamt rentabler zu machen.
Yaskawa ist mit 479 Mrd. Yen (rund 3,7 Mrd. Euro, zum Geschäftsjahresende 28. Februar 2022) Jahresumsatz ein global agierender Technologielieferant im Bereich Robotik, Antriebs- und Steuerungstechnik sowie bei Lösungen im Energiebereich. Gegründet 1915 in Japan, ist Yaskawa seit über 100 Jahren der Philosophie treu, Produkte höchster Qualität zu liefern, und hat sich damit eine weltweite Spitzenposition erarbeitet. Dabei hat sich Yaskawa vom Motorenhersteller zunächst zum Automatisierungsanbieter und schließlich über das Industrie-4.0-Konzept i3- Mechatronics zum Lösungsanbieter weiterentwickelt.
Die Geschäftsaktivitäten von Yaskawa bestehen aus Drives (Frequenzumrichter GA700), Motion Control (Servoantriebe und Servomotoren Sigma-7, Maschinensteuerungen), Robotics (Motoman Industrieroboter, Robotersysteme), System-Engineering (Generatoren und Konverter) sowie Information Technology (Software-basierende Produkte). Seit 2012 umfasst das YaskawaPortfolio dabei auch Steuerungstechnik, Visualisierungssysteme und Chip-Lösungen der ehemaligen VIPA GmbH in Herzogenaurach. Im Oktober 2019 wurde die Verschmelzung rechtskräftig abgeschlossen. Die Marke Profichip wird seitdem bei Yaskawa als eigene Produktsparte „Profichip Embedded Solutions“ weitergeführt. Darüber hinaus wurde im Oktober 2014 das in den Bereichen Wind-, Schiffs- und Turbo-/Industrieanwendungen tätige Unternehmen The Switch Engineering Ltd. von Yaskawa übernommen.
Damit ist Yaskawa weltweit eines von wenigen Unternehmen, das Komponenten und Lösungen für fast alle Branchen aus einem Haus anbieten kann.
Mit umfangreichen Investitionen in Forschung und Entwicklung hat das Unternehmen eine Vielzahl von Erfindungen, Patenten und Innovationen hervorgebracht. Dieser technologische Anspruch hat die Geschäftsbereiche zu einer bedeutenden Marktposition in verschiedenen Industrien geführt, darunter: Maschinenbau und Anlagenbau (Verpackungsmaschinen, Pumpen/Kompressoren, Textilmaschinen, Digitaldruckmaschinen, Herstellung von Kränen und Hebezeugen, Anlagen für Halbleiter- und Elektronikfertigung, Maschinen zur Gewinnung und Bearbeitung von Holz, Glas, Metall, Steine/Erden) sowie in der Aufzugs-Industrie, im Fahrzeugbau und in der Montage- und Handhabungstechnik. Industrieroboter der Marke Motoman finden zum Beispiel beim roboterbasierten Schweißen, in der Laborautomation, beim Verpacken und Handling sowie beim automatisierten Lackieren Anwendung.
Die Yaskawa Europe GmbH mit Sitz in Eschborn bei Frankfurt gliedert sich in die Geschäftsbereiche Drives Motion Controls (Automatisierung, Antriebs- und Steuerungstechnik), Robotics (Industrieroboter, Systeme) und Environmental Energy (Umwelttechnik) und betreut die Märkte Europa, Afrika, Mittlerer Osten sowie den Bereich der früheren Sowjetunion.
www.yaskawa.de
YASKAWA Europe GmbH
Philipp-Reis-Str. 6
65795 Hattersheim am Main
Telefon: +49 (6196) 569-300
Telefax: +49 (6196) 569-398
http://www.yaskawa.eu.com
Senior Marketing Assistant
Telefon: +49 (6196) 569-483
Fax: +49 (6196) 569-44483
E-Mail: Annette.Vorreiter@Yaskawa.eu.com