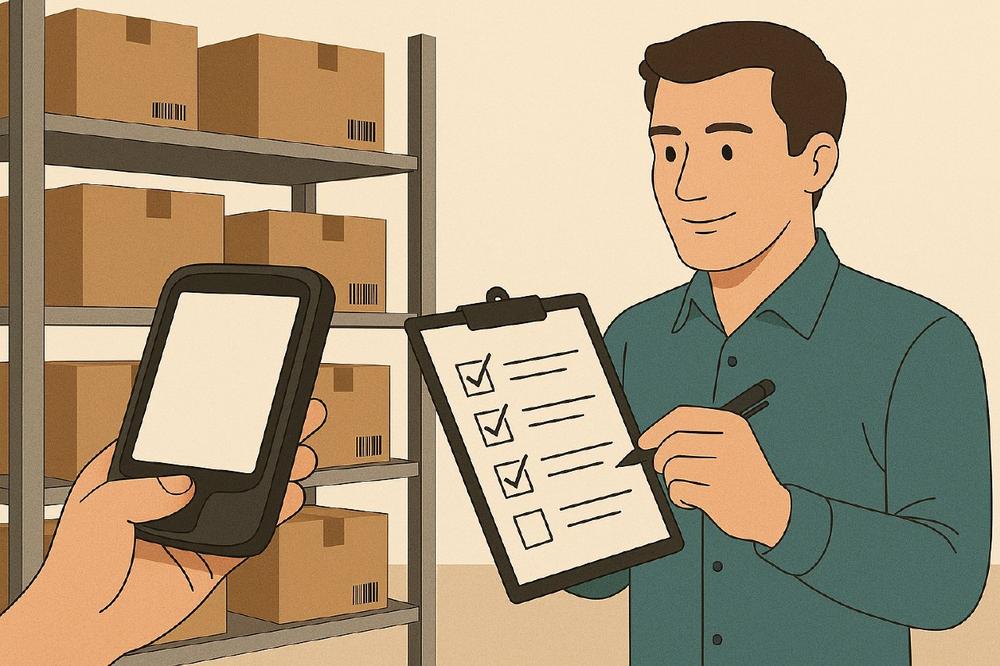
Taking inventory made simple: Importance and practical application
What is an inventory take? Definition and purpose
Taking inventory is a systematic process conducted annually to capture a company’s assets and liabilities for accounting and financial reporting purposes. This involves counting, measuring, or weighing various articles. The result of this process is the stock take list, which serves as a comprehensive record of all captured assets and forms the foundation for financial statements.
Why is taking inventory necessary?
According to section 240 of the German Commercial Code (HGB), every merchant is required to conduct a stock take at the beginning of business operations and at the end of each fiscal year. This ensures that all assets and liabilities are accurately documented in a clear and structured manner. Similar articles can be grouped together for simplified valuation.
Beyond compliance, inventory takes help businesses identify shortages, overstock, and losses due to theft or mismanagement. They also reveal bookkeeping errors or warehouse discrepancies, ensuring that captured stock levels match actual inventory.
Inventory taking methods/types
- Physical inventory takes
Taking inventory in physical manner involves capturing all tangible assets within a company by counting, measuring, or weighing them. It provides an accurate representation of actual stock levels and is typically conducted manually or with the help of digital tools.
[*] Book inventory takes
A book inventory take records non-physical assets, such as bank balances, receivables, payables, and liabilities. These values are determined using financial documents like bank statements, open invoice lists, and contracts rather than physical stock counts.
[*] Fixed asset inventory take
Taking inventory according to fixed assets accounts for all long-term assets that belong to a company’s fixed capital, such as machinery, buildings, vehicles, and technical equipment. These assets are tracked through visual inspection, inventory lists, or tagging systems.
Legally Approved Inventory Methods
- Annual Cut-Off inventory take
A cut-off inventory take is performed on a specific date—usually the company’s balance sheet date (e.g., December 31). However, businesses are given a 10-day window before or after this date to complete their inventory take.
[*] Shifted inventory take
If stock taking is conducted up to three months before or after the balance sheet date, it is classified as a shifted inventory take. In such cases, adjustments must be made to project stock levels as of the official reporting date.
[*] Perpetual inventory take
With a perpetual inventory system, stock levels are recorded continuously throughout the year instead of being counted once annually. This method helps maintain an up-to-date inventory record and reduces the need for large-scale year-end stock taking.
The process of taking inventory: Step-by-Step Guide
- Planning and Preparation
Selecting the right stock taking method is crucial for ensuring a smooth and accurate process. Key considerations include:
- The type of stock being counted
- The size of the company
- Legal requirements
A realistic timeline should be established, along with clear responsibilities for employees involved in the process. Training staff properly helps minimize errors and ensures a seamless execution. Additionally, warehouse organization should be optimized before starting to facilitate easier counting.
[*] Stock Capturing
The actual stock taking process involves physically capturing inventory, either manually or with barcode scanners. Items are counted, measured, or weighed, depending on their type. Data is then carefully documented—either using traditional paper-based methods or digital inventory management systems.
[*] Reconciliation and Quality Control
Once stock data has been captured, it is compared against existing records to identify discrepancies such as:
✔ Missing articles
✔ Overstocked products
✔ Data entry errors
This allows for quick adjustments and targeted investigations into stock discrepancies.
[*] Evaluation and Finalization
The last step involves:
- Analyzing inventory discrepancies
- Adjusting accounting records accordingly
- Generating a comprehensive inventory take report
- Identifying opportunities for process improvements
All relevant documentation is then archived in compliance with legal requirements.
How inventory taking software optimizes the process
The inventory taking software by COSYS is a fully digital solution designed to simplify and automate inventory takes. The system consists of a mobile stock taking app and a backend platform that seamlessly integrates with warehouse operations.
Key features of the inventory taking software by COSYS:
✔ Mobile Data Capture – Use smartphones or mobile computers to scan stock articles and conduct counts efficiently.
✔ Real-Time Data Transfer – inventory take data is immediately uploaded to the COSYS WebDesk, where it can be monitored and analyzed.
✔ Error Reduction – Automated scanning minimizes human errors, reducing miscounts, duplicates, and misplaced articles.
✔ Offline Capability – If there’s no network connection, data is safely stored on the device and automatically synchronized once connectivity is restored.
✔ Seamless ERP Integration – COSYS integrates smoothly with any enterprise resource planning (ERP) system for streamlined inventory take management.
✔ User-Friendly Interface – Designed for quick onboarding, allowing new employees to participate with minimal training.
Upgrade Your inventory taking process with COSYS!
COSYS Ident GmbH, based in Grasdorf (near Hildesheim), has been in existence for almost 40 years and is one of the leading system houses in the field of mobile data capture solutions for Android and Windows. A medium-sized company that has been driving the development of identification systems since 1982 and today offers industry-specific complete solutions for almost all common business processes. From process design and concept development to hardware and software implementation, project management and customized maintenance contracts, we cover the entire range of system development, integration and support services. COSYS also offers a repair service, WLAN radio measurement and solutions for component traceability using DPM codes.
Cosys Ident GmbH
Am Kronsberg 1
31188 Holle – Grasdorf
Telefon: +49 (5062) 900-0
Telefax: +49 (5062) 900-30
http://www.cosys.de
Telefon: +49 (5062) 900-0
E-Mail: vertrieb@cosys.de

