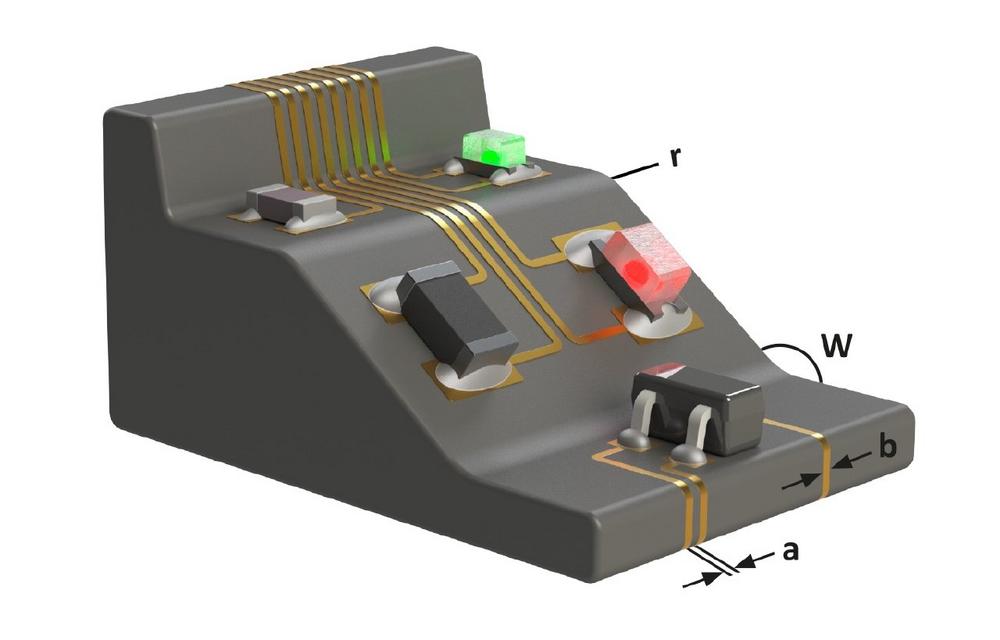
Elektronikbaugruppen ohne Leiterplatten
Die Laserdirektstrukturierung (LDS) ist eine besondere Erfolgsgeschichte. Seit knapp 20 Jahren können elektronische Leiterbahnen in der Serienherstellung direkt auf Kunststoffteile aufgebracht werden.
Laser Direct Structuring (LDS) – Die Struktur der Leiterbahn wird durch das LDS-Verfahren aufgebracht. LDS ermöglicht Elektronikbaugruppen mit flexiblen geometrischen Formen. Dank dieses Verfahrens werden Handys, Hörgeräte oder Smartwatches immer kleiner und leistungsfähiger.
LDS ermöglicht Elektronikbaugruppen mit flexiblen geometrischen Formen. Dank dieses Verfahrens werden elektronische Produkte wie Smartphones, Sensoren oder medizinische Geräte immer kleiner und leistungsfähiger. Automatisierte Herstellungsprozesse machen das Verfahren zudem wirtschaftlich immer attraktiver.
Für elektronische Baugruppen bleibt immer weniger Platz, so dass nach Lösungen gesucht wird, um konventionelle Leiterplatten zu ersetzen. LDS ermöglicht die weitere Miniaturisierung und immer komplexere geometrische Bauformen. Das Verfahren ist prozessstabil und zuverlässig und hat sich auch in besonders qualitätskritischen Bereichen wie der Medizintechnik oder bei sicherheitsrelevanten Komponenten für die Automobilindustrie durchgesetzt.
Das LDS-Verfahren ermöglicht dreidimensionale Baugruppen
Die Laserdirektstrukturierung macht 3D-MID-Baugruppen (Mechatronic Integrated Devices) möglich. Durch 3D-MID können elektronische Bauteile direkt auf einen dreidimensionalen Grundkörper bestückt werden, ohne Leiterplatten und Verbindungskabel. Der Grundkörper wird im Spritzgussverfahren hergestellt, wobei der thermoplastische Kunststoff mit einem nicht leitenden, anorganischen Additiv versehen wird.
Damit das Kunststoffmaterial elektrische Leiterbahnen aufnehmen kann, werden die Additive im Material durch die Laserdirektstrukturierung „aktiviert“. Dabei beschreibt der Laserstrahl die für die Leiterbahnen vorgesehenen Flächen und es entsteht eine mikroraue Struktur. Die freigesetzten Metallpartikel bilden die Kerne für die anschließende chemische Metallisierung. Auf diese Weise werden auf den vom Laser markierten Flächen elektrische Leiterbahnen aufgebracht. Die anderen Bereiche des dreidimensionalen Grundkörpers bleiben unverändert. Das Kunststoffbauteil kann anschließend wie eine herkömmliche Leiterplatte in Standard-SMD-Prozessen bestückt werden und ist auch für den Lötprozess im Reflow-Ofen geeignet.
Lasertechnik ist flexibel einsetzbar
HARTING 3D-MID AG ist der größte Lieferant von 3D-MID-Komponenten außerhalb Asiens. Für das LDSVerfahren setzt HARTING Hochleistungs-Lasersysteme mit drei parallel arbeitenden Lasern ein, die jeweils um 45 Grad versetzt angeordnet sind. Durch die zusätzliche Drehachse können Bauteile durch den Laser gleichzeitig von allen Seiten in 360 Grad bearbeitet werden. Durch diese Technik werden flexible geometrische Formen möglich, wie bei Reflektorschalen oder für LED-Leuchten. Trotz der geringen Leiterbahnstärke von 16 bis 20 μm eignen sich die Leiterbahnen für anspruchsvolle Automotive-Komponenten oder für Anwendungen mit Stromstärken bis zu 10 A wie zum Bespiel für Heizwendeln bei Kameras, die ein Beschlagen der Optik verhindern.
Dimensionierung und Position – Minimalwert für Abstände zwischen den Leiterbahnen (a): 150 μm Minimale Bereite der Leiterbahnen (b): 150 – 250 μm
Radius (r): 0,2 mm
Häufige Änderungen während der Elektronikentwicklung oder neue Bauteile mit veränderten Abmaßen führen bei der konventionellen PCB-Herstellung zu aufwendigen Anpassungen. Das Laserlayout lässt sich durch Eingaben in der Steuerungssoftware des Lasers dagegen sehr flexibel anpassen. Änderungen im Spritzguss sind dafür nicht notwendig.
Im Vergleich mit herkömmlichen Verfahren ist auch die Herstellung von Prototypen bei LDS einfacher. HARTING kann die Kunststoffgrundkörper mit Hilfe von LDS-fähigem Material im 3D-Druck herstellen. Zum Einsatz kommt auch ein Spritzguss mit kostengünstigen Prototypen-Werkzeugen.
Neue Trends beim LDS-Verfahren
Die LDS-Technologie wurde in den letzten Jahren gleich in mehreren Bereichen verbessert und weiterentwickelt:
– Der Arbeitsbereich der Laser wurde von 160 x 160 x 80mm auf 200 mm x 200 mm x 80 mm vergrößert, was eine höhere Packungsdichte oder die Bearbeitung noch größerer Teile ermöglicht.
– Die Arbeitsgeschwindigkeit des Lasers konnte durch Optimierung der Servoeinheiten und Spiegeln für die Führung des Laserstrahls auf 4 m/s verdoppelt und die Bearbeitungszeit somit deutlich verringert werden.
– Die Verbesserung der Optiken ermöglicht neben einem Laser mit einem Durchmesser von 100 μm auch einen Laser mit einem Feinfokus von 50 μm für die Bearbeitung noch kleinerer Strukturen.
HARTING ist der einzige 3D-MID-Produzent weltweit, der über ein Lasersystem mit drei Feinfokus-Optiken von 50 μm verfügt. Durch den Feinfokus-Laser werden nochmals geringere Leiterbahnabstände erreicht. So kann auf dem gleichen Bauteil eine größere Anzahl an Leiterbahnen erstellt und eine höhere Packungsdichte erreicht werden. Sie wird u.a. für Sicherheitstechniken genutzt, weil die eng nebeneinander liegenden und verschlungenen Leiterbahnen selbst bei kleinsten physischen Eingriffen Sicherheitsalarme auslösen.
Fortschritte beim Material und bei der Wirtschaftlichkeit
Für das LDS-Verfahren sind nur ausgewählte thermoplastische Kunststoffe zertifiziert und ab Lager verfügbar. Weitere Verbesserungen des Verfahrens betreffen kundenspezifische Anpassungen beim Kunststoff-Material:
– HARTING nutzt ein Verfahren, um auch nicht zertifizierte Werkstoffe durch LDS-Additive MID-tauglich zu machen.
– Durch Farbpigmente und spezielle LDS-Additive lassen sich bei MID-Kunststoffen spezifische RALoder Pantone-Farbtöne erreichen.
– Durch die Auswahl geeigneter Additive können je nach Frequenzbereich auch besondere RFEigenschaften erzeugt werden.
Bauteilträger – Elektronische Bauteile, wie LEDs, ICs, Fotodioden und Sensoren werden direkt auf den Bauteilträger bestückt. Anschließend lassen sich die bestückten Bauteilträger wie Standard-SMDKomponenten verarbeiten.
Um die Wirtschaftlichkeit des Herstellprozesses weiter zu verbessern, setzt HARTING auf die Automatisierung durch Robotersysteme. Die LDS-Lasersysteme sind mit einem Rundschalttisch ausgerüstet, damit ein Bauteil eingelegt bzw. entnommen werden kann, während ein anderes Bauteil noch bearbeitet wird. Das Zuführen und Entnehmen wird bei HARTING durch Robotertechnik automatisiert. So wird der Durchsatz und die Autonomie erhöht und eine Integration in automatisierte Produktionsabläufe ermöglicht. Einen weiteren Automatisierungsschritt nutzt der Dienstleister beim Spritzgussverfahren. Auch hier übernimmt ein Roboter das Entnehmen von Spritzgussteilen. Der Robotereinsatz erhöht zudem die exakte Reproduzierbarkeit der Prozesse und verbessert damit auch die Produktqualität.
Weiteres Wachstum für 3D-MID
Sicherheitskappen für Zahlungsterminals – Die Sicherheitskappen von HARTING schützen das Auslesen von Kreditkarteninformationen. Die 3D-MID Kappen schützen die Elektronik mechanisch und elektronisch vor unautorisiertem Zugriff. Eine hochpräzise Mäanderstruktur detektiert jeden noch so kleinen Eingriff und verhindert somit den Datendiebstahl.
HARTING berichtet von steigenden Anfragen für MID-Projekte und hat den Geschäftsbereich 3D-MID durch Investitionen in den Maschinenpark und durch die Übernahme der Geschäftstätigkeiten eines Wettbewerbers weiter ausgebaut. Zum weiteren Wachstum tragen auch innovative Eigenprodukte bei. HARTING hat basierend auf der 3D-MID-Technologie eine Lösung entwickelt, die Flex-Leiterplatten durch einen Bauteilträger ersetzen kann. Der Bauteilträger kann anstelle der Flex-Leiterkarte direkt mit elektronischen Bauteilen bestückt werden und somit bis zu zwei Drittel der Kosten einsparen.
HARTING 3D-MID bietet die vollständige Wertschöpfungskette für 3D-MID-Technologien unter einem Dach, einschl. Entwicklung/ Prototyping von kundenspezifischen Produkten, Spritzguss, Laserdirektstrukturierung, Metallisierung, Aufbau- und Verbindungstechnik und Endprüfung. Kerngeschäft ist die Produktion mechatronischer Komponenten für Automobilbau, Industrie, Medizintechnik und Sensorik. HARTING ist der größte Lieferant von 3D-MID-Komponenten außerhalb Asiens. HARTING 3D-MID ist ein Geschäftsbereich der HARTING Technologiegruppe, mit Sitz in Espelkamp, Deutschland.
HARTING AG
Leugenestrasse 10
CH2500 Biel 6
Telefon: +41 (32) 3442121
Telefax: +41 (32) 3442122
https://harting.com/DE/de
HARTING AG
Telefon: +41 (76) 3909-074
E-Mail: Thomas.Hess@HARTING.com
MEPAX
Telefon: +34 (620) 065-719
E-Mail: l.gordon@mepax.com
